Floor Cleaning Equipment Parts
INDUSTRIAL FLOOR SCRUBBER & SWEEPER PARTS & ACCESSORIES
High-Quality Floor Cleaning Machine Parts from a Leading Supplier
Maximize Your Equipment’s Lifespan with Our Premium Replacement Parts
At CY Cleaning Equipment, we understand how crucial your floor cleaning machines are to the success of your business. That’s why we provide only the best parts and accessories for your scrubbers and sweepers. Our range includes brushes, batteries, pads, filters, and more—all designed to keep your machines running at peak performance for longer.
Explore our extensive selection of high-quality ORIGINAL CY industrial and commercial floor scrubber and sweeper parts designed for optimal performance and longevity.
Find the perfect match for your equipment with our durable ORIGINAL brushes, squeegees, batteries, and more. Upgrade and maintain your scrubbers and sweepers today for uninterrupted cleaning efficiency.
CATEGORIES
Batteries & Accessories
Bearings
Brush Motors & Acc
Brushes & Accessories
Burnisher Engine Parts
Chargers & Acc
Drive Components
Electrical
Filters
Hardware
Hoses and Cuffs
Lids & Gaskets
Pads & Pad Drivers
Propane Equip Parts
Pumps
Solution Tank & Acc
Squeegees & Skirts
Surface Prep
Switches
Vacuum Motors
Valves
Wheels and Tires
FEATURED PRODUCTS
INDUSTRIAL FLOOR SCRUBBER & SWEEPER PARTS & ACCESSORIES
High-quality ORIGINAL CY Parts and Accessories
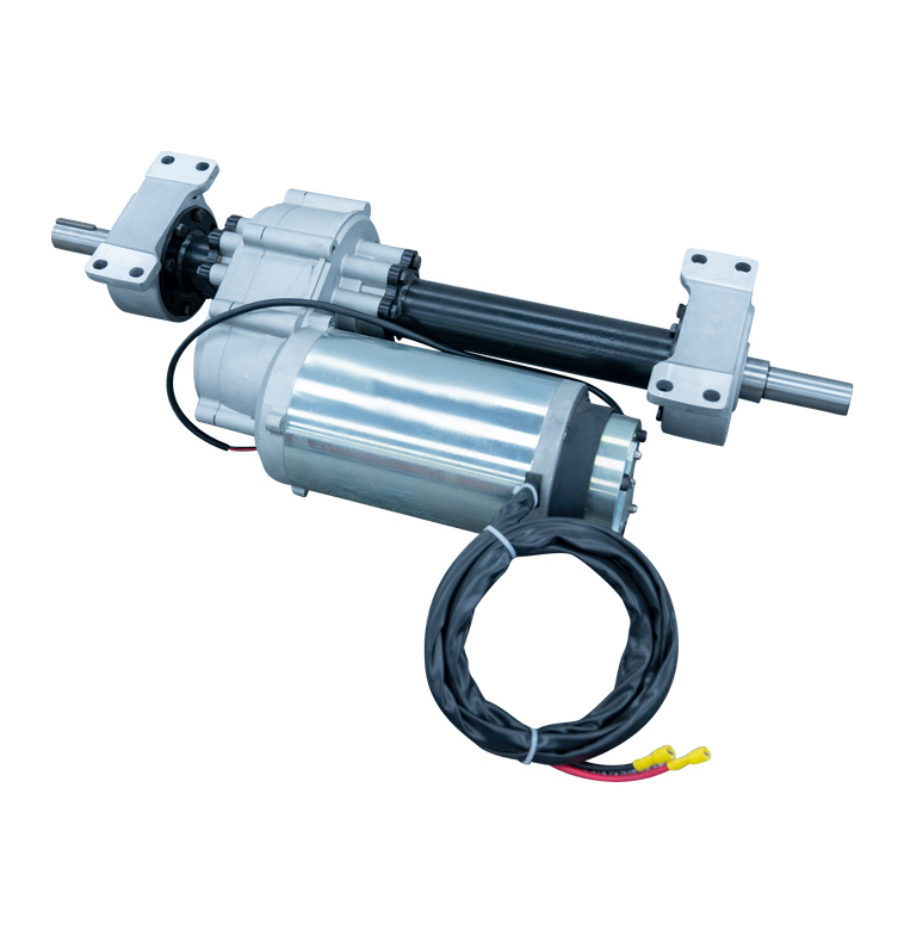
Actuators
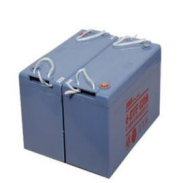
Batteries & Accessories
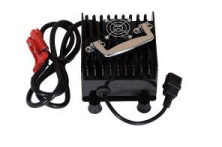
Chargers & Acc
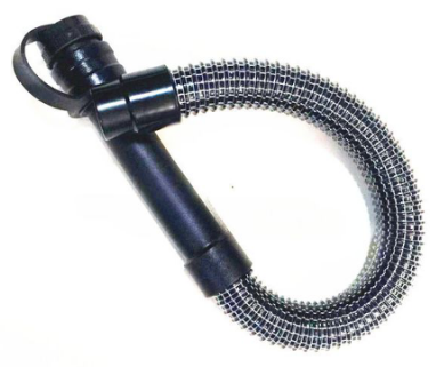
Hoses and Cuffs
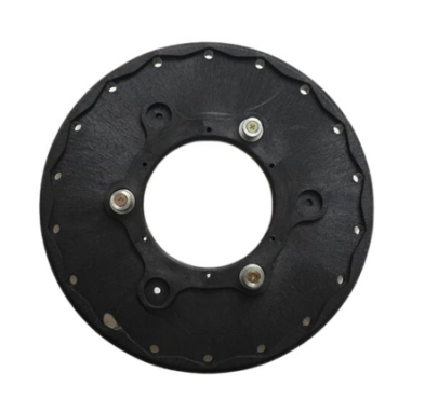
Pads & Pad Drivers
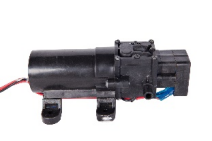
Pumps
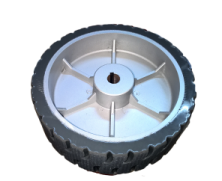
Wheels and Tires
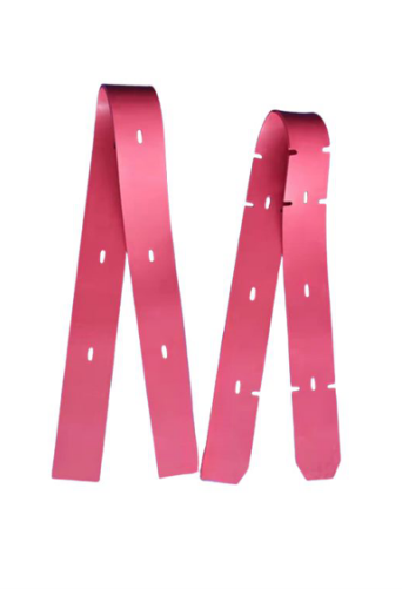
Squeegees & Skirts
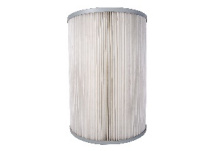
Filters

Brush Motors & Acc
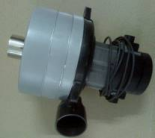
Vacuum Motors
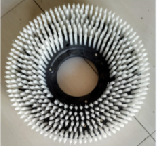
Brushes & Accessories
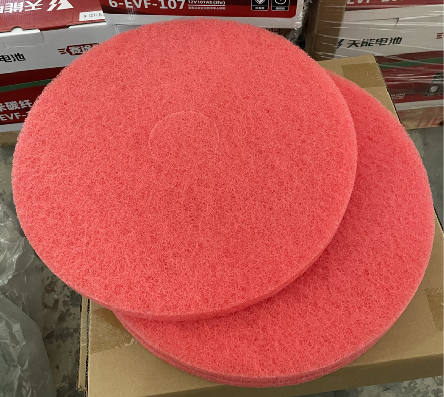
Pad
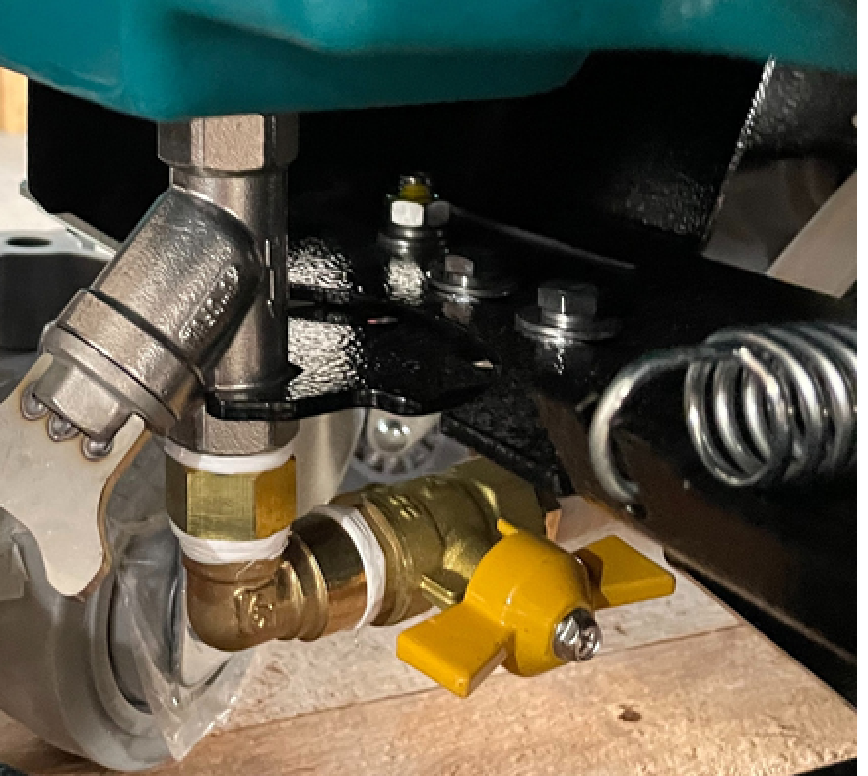
Vacuum Motors
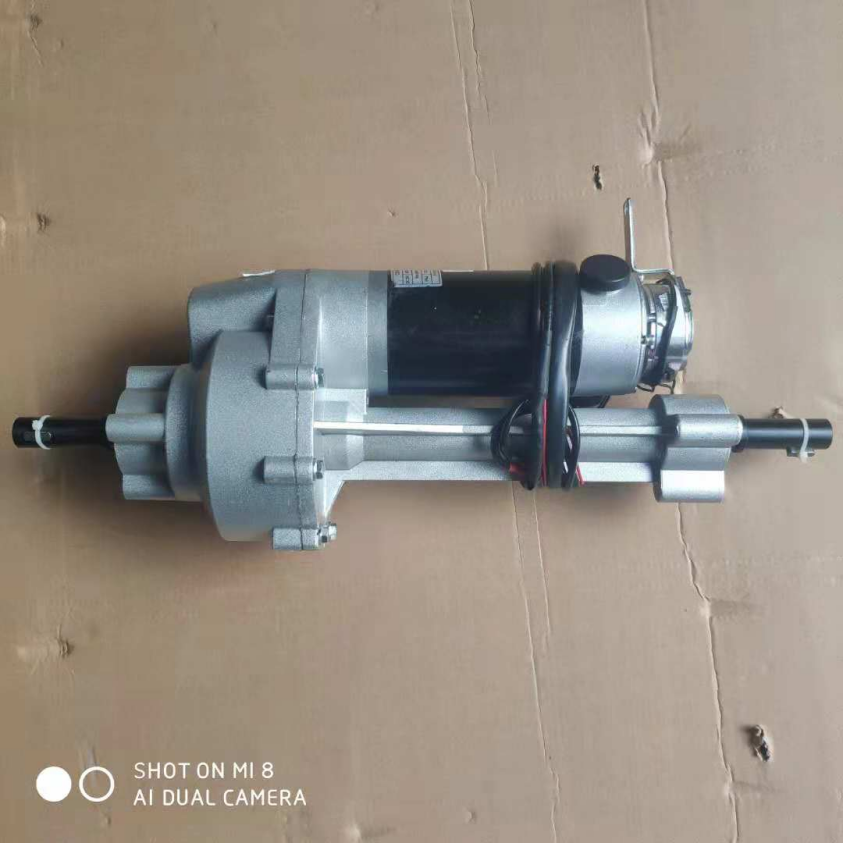
Drive Components

Brush Motors & Acc
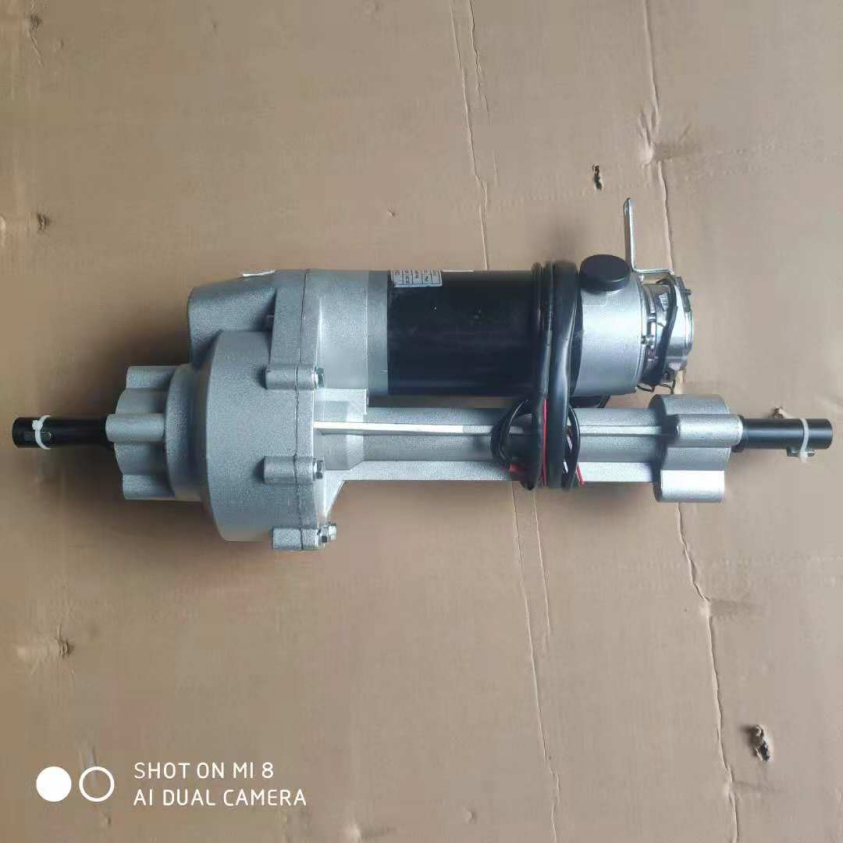
Drive Components
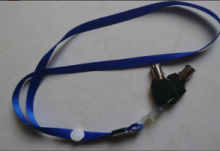
Switches
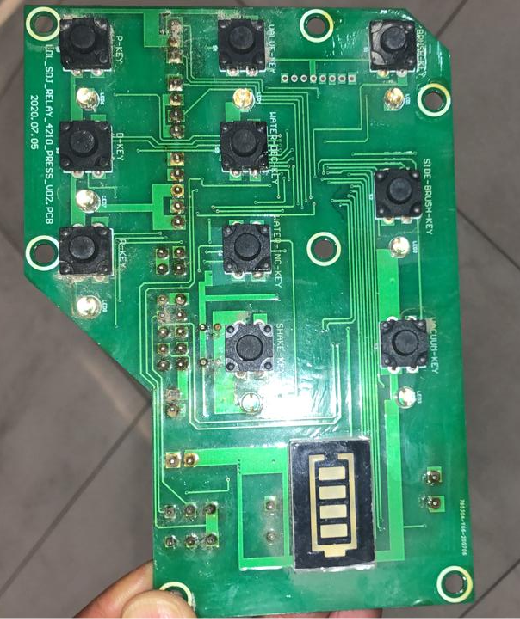
Electrical
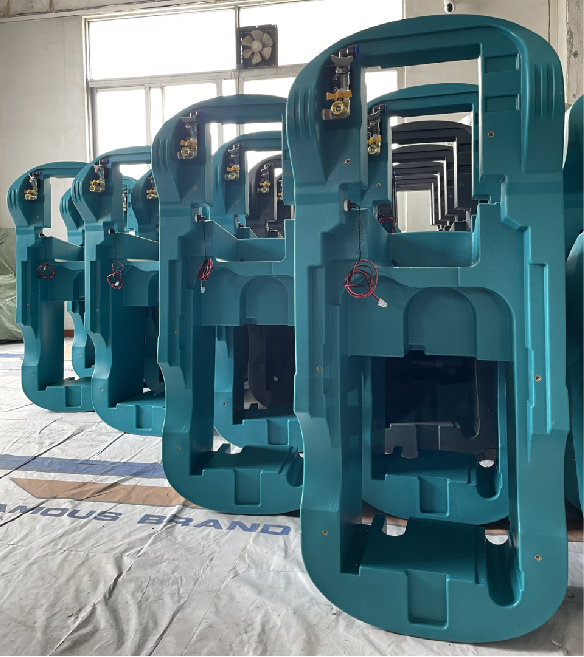
Solution Tank & Acc
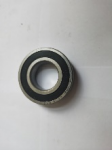
Bearings
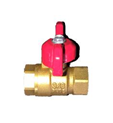
Valves
Unique Features:
Our parts are sourced from trusted manufacturers and are built to last. With an emphasis on reliability and performance, our accessories ensure your floor cleaning machines continue to operate efficiently for years.
Customer Review:

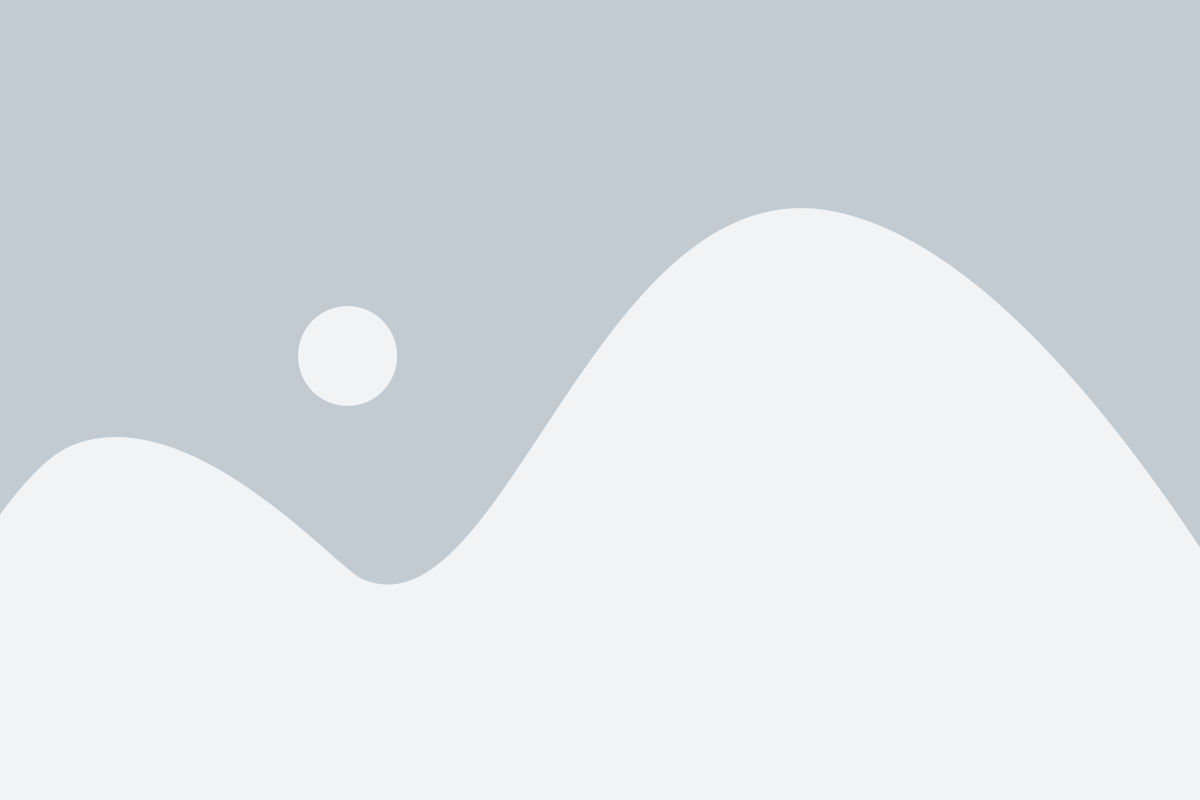
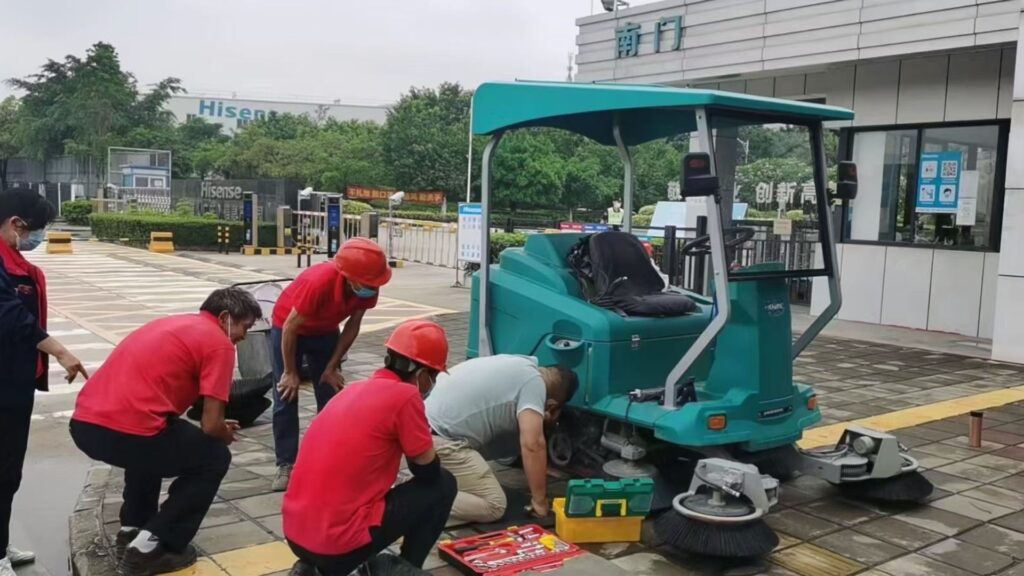
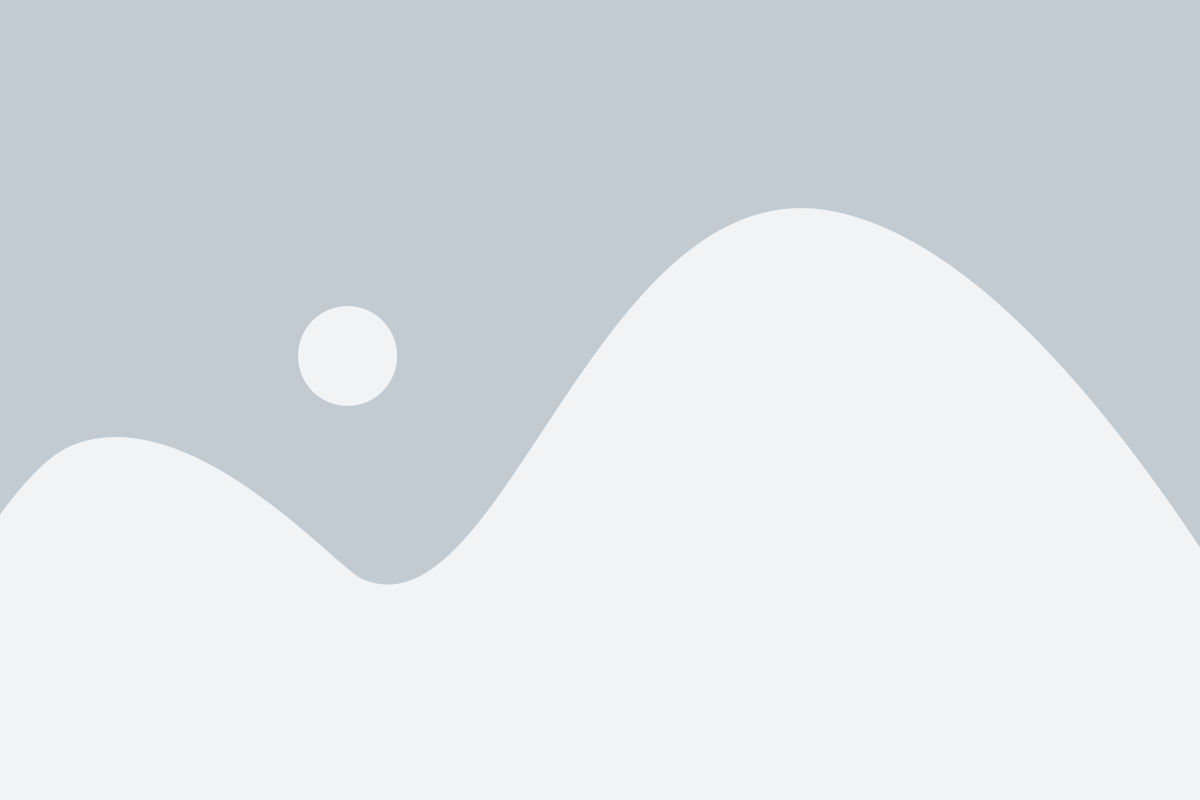
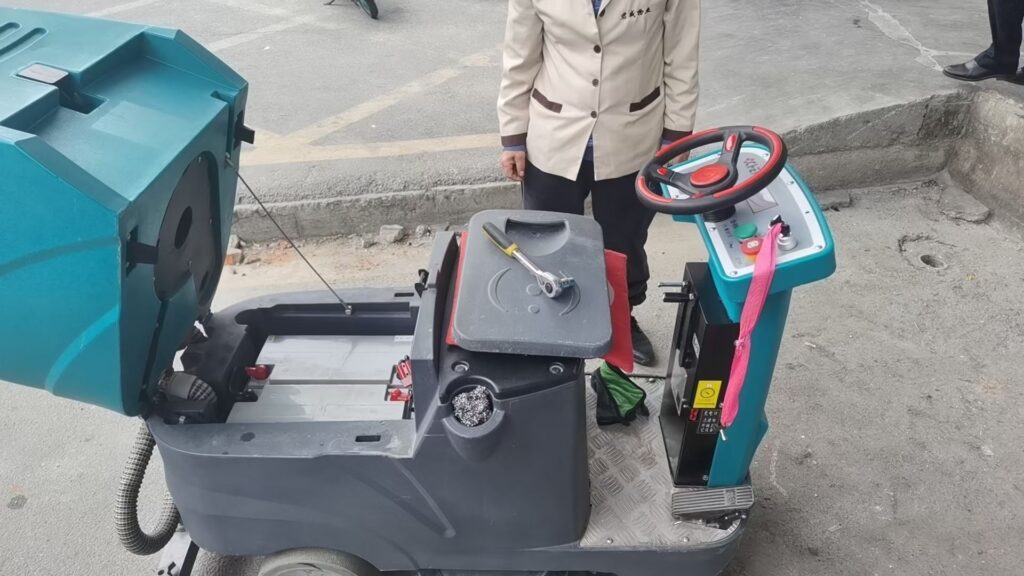
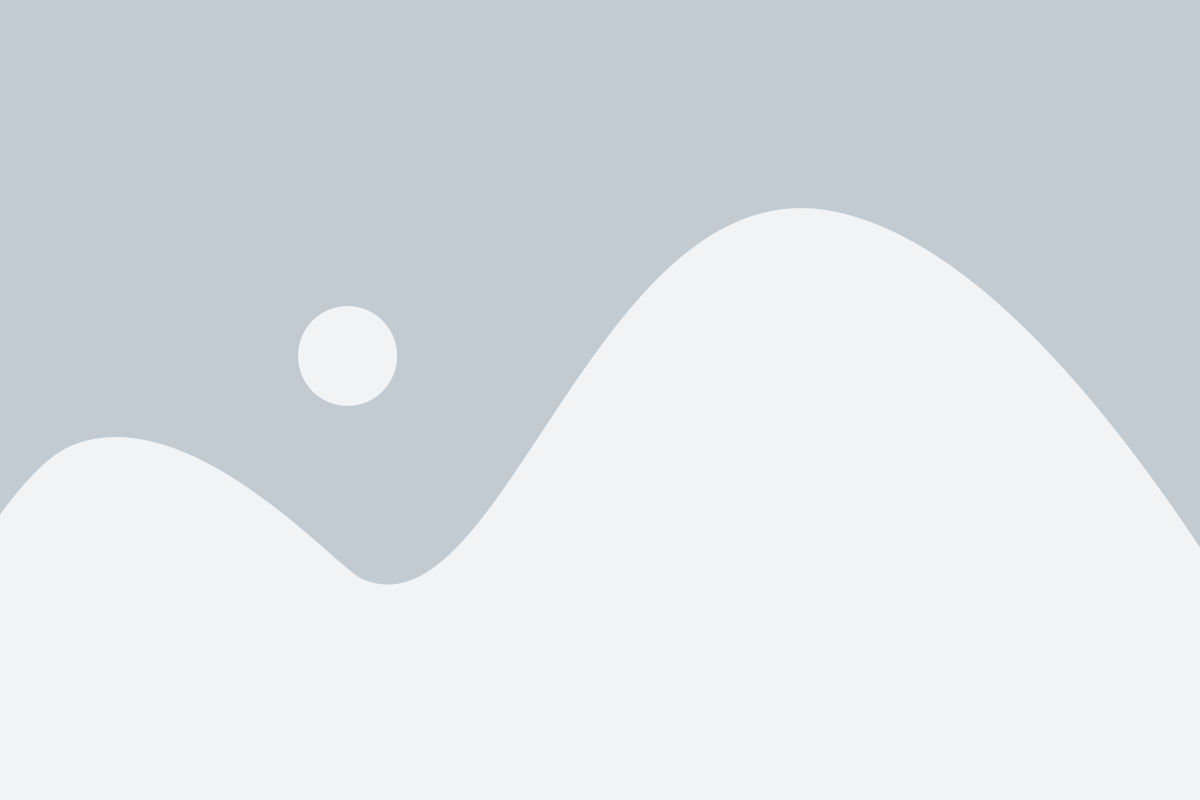
INDUSTRIAL FLOOR SCRUBBER & SWEEPER PARTS & ACCESSORIES GUIDE
When it comes to industrial floor scrubbers and sweepers, understanding the parts and accessories that keep them running smoothly is crucial. Whether managing a fleet of machines or just one, this guide will help you identify essential components, highlight differences between high-end and mid-range models, and offer practical tips to save costs while ensuring reliability.
Key Components and Wear Parts for Floor Scrubbers & Sweepers
Industrial cleaning machines, regardless of brand, rely on several critical parts. Here’s a breakdown of the most common components:
- Squeegees
- Function: Ensures water and cleaning solution are efficiently removed from the floor.
- Wear & Maintenance: Made from rubber or polyurethane, these parts wear out quickly due to friction.
- Brushes
- Types: Scrubbing brushes (disk or cylindrical), sweeping brushes.
- Materials: Nylon, polypropylene, or abrasive materials for tough surfaces.
- Replacement: Varies based on usage frequency and surface type.
- Filters
- Role: Protects the machine by filtering debris and dirt.
- Maintenance: Regular cleaning ensures optimal suction and airflow.
- Vacuum Motors
- Purpose: Powers the suction mechanism.
- Wear Points: Filters and motor seals should be checked regularly.
- Batteries
- Common Type: Lead-acid or lithium-ion.
- Lifespan: Depends on charging cycles and maintenance.
- Hoses and Tubes
- Usage: Transport cleaning solution and suction debris.
- Maintenance Tip: Look for cracks or clogs regularly.
- Solution Tanks & Recovery Tanks
- Care: Clean these tanks daily to prevent mold or residue buildup.
- Wheels and Casters
- Importance: Mobility and stability of the machine.
- Maintenance: Regular inspection for cracks or wear.
High-End Brands and Their Maintenance Needs
Brands like Hako, Tennant, Karcher, IPC, Tomcat, and CY set the gold standard for industrial cleaning machines. Their parts are engineered for durability and performance, but maintenance still plays a key role in ensuring longevity.
Parts Commonly Needed for High-End Machines
- Premium Brushes and Squeegees: Designed for efficiency, often with longer lifespans than budget alternatives.
- High-Capacity Batteries: Lithium-ion options are common for extended runtimes.
- Advanced Control Systems: Brands like CY use imported controllers for reliability.
- Noise-Reduction Components: For low-noise operations.
- Specialized Filters: Often HEPA-grade for superior air quality.
Why They Stand Out
- Durability: High-end machines use robust materials that reduce the frequency of part replacements.
- Performance: Enhanced features, such as precise water flow control, improve cleaning efficiency.
- Support: Professional after-sales service ensures timely repairs and access to genuine parts.
Mid-Range and Budget Machines: Parts & Maintenance
While more affordable, mid-range and budget floor scrubbers often require more frequent maintenance and part replacements.
Common Parts for Budget Machines
- Standard Brushes and Squeegees: Affordable but wear out faster.
- Basic Batteries: Typically lead-acid with shorter lifespans.
- Simpler Control Panels: Easier to operate but may lack advanced diagnostics.
- Lower-Quality Filters and Hoses: Prone to clog or wear.
Challenges with Budget Machines
- Frequent Downtime: Due to faster wear and tear of parts.
- Higher Long-Term Costs: Repeated part replacements can add up.
- Limited Features: It may lack noise reduction, robust build, or extended battery life.
Key Differences Between High-End and Budget Machines
Feature | High-End Machines | Mid-Range/Budget Machines |
---|---|---|
Part Lifespan | Longer (e.g., brushes lasting 2-3 years) | Shorter (e.g., brushes lasting 6-12 months) |
Part Quality | Premium materials | Basic materials |
Maintenance Frequency | Lower | Higher |
Operating Cost | Lower over time | Higher due to frequent replacements |
Initial Cost | Higher upfront investment | Lower upfront investment |
How to Buy Reliable Floor Scrubber Parts
- Choose Genuine Parts
- Always opt for manufacturer-recommended parts for compatibility and reliability.
- Research Trusted Suppliers
- Look for suppliers with strong reviews and a proven track record.
- Consider Durability Over Cost
- Cheaper parts may save money now but cost more in frequent replacements.
- Bulk Purchasing
- Stock up on frequently replaced items like brushes and squeegees to save on shipping and bulk discounts.
Controlling Maintenance Costs
- Preventive Maintenance
- Regularly inspect and clean components to extend their life.
- Operator Training
- Ensure staff knows how to use and maintain machines properly to reduce avoidable wear.
- Invest in Quality Machines
- Machines like CY scrubbers, known for their imported controllers and stable performance, are a good long-term investment.
What Makes a Scrubber “Good Value”?
A truly good value floor scrubber is more than just a low price tag. It delivers long-term savings and peace of mind.
Here’s what to look for:
- Reasonable Purchase Price
- Reliable Quality: For instance, CY scrubbers use imported controllers for stability and a lifespan of 5+ years.
- Low Noise Levels: Essential for hospitals, schools, and office settings.
- Ease of Use: Machines that are intuitive reduce training time.
- Low Maintenance Costs: Durable parts and minimal breakdowns keep costs in check.
- Long Battery Life: Extended operation between charges.
- Timely After-Sales Service: A reliable service network is vital for repairs.
- Strong Reputation: Brands with positive industry feedback inspire confidence.
Conclusion
Investing in the right floor scrubber parts and accessories can significantly impact your machine’s performance and maintenance costs. Whether you’re using high-end machines like Hako or Tennant or managing mid-range options, knowing the differences and making informed choices ensures optimal performance and cost efficiency.
Remember, a good value scrubber isn’t just about the price—it’s about reliability, ease of maintenance, and long-term benefits. By following this guide, you’ll be well-equipped to make smart decisions for your cleaning operations.
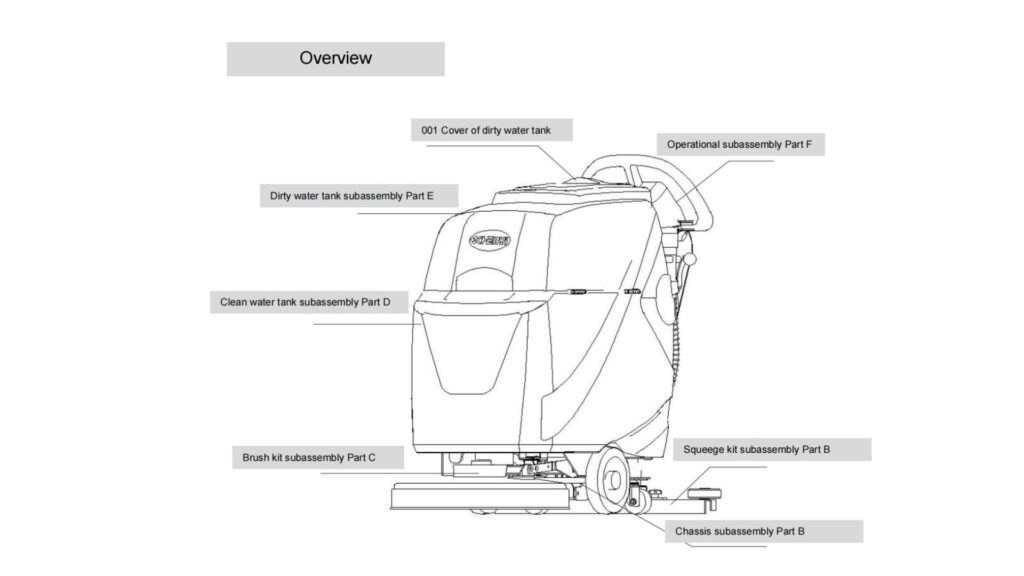
Walk-Behind Scrubber Maintenance and Repair Spare Parts Checklist That Should Be in Stock: Reduce Downtime & Save Repair Costs
Essential Walk-Behind Scrubber Spare Parts to Keep in Stock
To help you stay prepared, here’s a comprehensive list of essential replacement parts you should always have in your inventory for walk-behind scrubbers, their average usage lifespan, and the suggested quantities you should keep in stock for the next 2-3 years (based on a medium-sized facility using a scrubber regularly).
Spare Part | Usage Lifespan | Signs of Wear/Failure | Suggested Quantity for 2-3 Years | Where to Buy |
---|---|---|---|---|
Squeegee Blades | 6–12 months | Water streaks, excessive water on the floor, cracked or torn blades | 4-6 sets (1 set every 6 months) | Shop Squeegee Blades |
Brushes & Scrub Pads | Brushes: 6–12 months, Scrub Pads: 3–6 months | Poor cleaning performance, frayed bristles or pads | 6-8 sets (2-3 sets per year) | Shop Brushes & Scrub Pads |
Batteries | 2–5 years | Short battery life, doesn’t hold a charge, slow to charge | 2-3 batteries (1-2 every 2-3 years) | Shop Batteries |
Vacuum Motors | 3–5 years | Reduced suction, strange sounds, water left behind | 1-2 motors (1 every 3-5 years) | Shop Vacuum Motors |
Drive Belts & Transmission | Drive Belts: 1–2 years, Transmission: 3–5 years | Erratic movement, squealing or grinding sounds, slow movement | 2-4 drive belts, 1 transmission | Shop Drive Belts & Transmissions |
Recovery Tank Filters | 6–12 months | Reduced suction power, debris in the recovery tank, frequent clogs | 4-6 filters (1 set every 6 months) | Shop Recovery Tank Filters |
Circuit Boards | 5–7 years | Scrubber won’t start, irregular operation, error codes | 1 circuit board (every 5-7 years) | Shop Circuit Boards |
Reduce downtime and save on repair costs with our ultimate checklist for walk-behind scrubber maintenance and spare parts. Ensure your equipment is always ready for use!
Maintaining your walk-behind scrubber is essential to keep it running efficiently and avoid costly repairs or downtime. As a facility manager, you know how important it is to have the right spare parts on hand to ensure the longevity of your equipment. Whether you’re running a warehouse, cleaning large retail spaces, or managing a school or hospital, proper upkeep of your scrubbers will not only save you money but also increase the productivity of your team.
In this guide, we’ll walk through the must-have spare parts for your walk-behind scrubber, what to keep in stock, and how you can reduce downtime and repair costs by staying prepared.
The Importance of Keeping Spare Parts in Stock
When you’re responsible for the cleanliness of a large facility, the last thing you want is for your equipment to break down during peak hours. Having the right spare parts on hand helps you address issues quickly and minimizes the amount of downtime you experience.
Here’s why it’s so important:
- Prevent Unexpected Costs: Having a spare part ready to go reduces the chances of having to pay for expedited shipping or costly emergency repairs.
- Maximize Equipment Lifespan: Regularly replacing worn-out parts helps extend the life of your scrubber.
- Minimize Facility Disruptions: Quick repairs mean your facility stays clean without unnecessary delays.
- Optimize Cleaning Performance: Proper maintenance ensures that your scrubber continues to work as efficiently as possible, saving time and energy.
Essential Walk-Behind Scrubber Spare Parts to Keep in Stock
To help you stay prepared, here’s a comprehensive list of essential replacement parts you should always have in your inventory for walk-behind scrubbers, their average usage lifespan, and the suggested quantities you should keep in stock for the next 2-3 years (based on a medium-sized facility using a scrubber regularly).
Spare Part | Usage Lifespan | Signs of Wear/Failure | Suggested Quantity for 2-3 Years | Where to Buy |
---|---|---|---|---|
Squeegee Blades | 6–12 months | Water streaks, excessive water on the floor, cracked or torn blades | 4-6 sets (1 set every 6 months) | Shop Squeegee Blades |
Brushes & Scrub Pads | Brushes: 6–12 months, Scrub Pads: 3–6 months | Poor cleaning performance, frayed bristles or pads | 6-8 sets (2-3 sets per year) | Shop Brushes & Scrub Pads |
Batteries | 2–5 years | Short battery life, doesn’t hold a charge, slow to charge | 2-3 batteries (1-2 every 2-3 years) | Shop Batteries |
Vacuum Motors | 3–5 years | Reduced suction, strange sounds, water left behind | 1-2 motors (1 every 3-5 years) | Shop Vacuum Motors |
Drive Belts & Transmission | Drive Belts: 1–2 years, Transmission: 3–5 years | Erratic movement, squealing or grinding sounds, slow movement | 2-4 drive belts, 1 transmission | Shop Drive Belts & Transmissions |
Recovery Tank Filters | 6–12 months | Reduced suction power, debris in the recovery tank, frequent clogs | 4-6 filters (1 set every 6 months) | Shop Recovery Tank Filters |
Circuit Boards | 5–7 years | Scrubber won’t start, irregular operation, error codes | 1 circuit board (every 5-7 years) | Shop Circuit Boards |
How to Manage Your Spare Parts Inventory
Proper inventory management is key to reducing downtime and ensuring your scrubber is always operational. Here are a few tips for staying organized and stocked up:
- Track the Frequency of Repairs: Keep a log of the parts that are replaced most often. This will give you an idea of which parts you should prioritize keeping in stock.
- Maintain a Reorder Point: Set up an automatic reorder point for key components like batteries and squeegee blades to avoid running out when you need them most.
- Keep Track of Your Models: Different models of scrubbers may require different parts, so ensure your inventory matches the models used in your facility.
- Store Parts Properly: Ensure parts are stored in a clean, dry environment to maintain their quality until you need them.
Where to Buy Walk-Behind Scrubber Parts
When it comes to purchasing parts, buying from trusted sources ensures you get high-quality products at the right price. You can find all the walk-behind scrubber parts you need at CY Cleaning Equipment.
Contact us for high-quality parts, including squeegee blades, batteries, brushes, and more.
Downloadable Checklist: Must-Have Spare Parts for Your Walk-Behind Scrubber
To help you stay organized, we’ve created a downloadable checklist of essential parts that should always be in stock. This checklist is perfect for facility managers and maintenance teams looking to avoid downtime and costly repairs.
Contact us for the Spare Parts Checklist
Need Help Finding the Right Part? Contact Us Today!
Maintaining your walk-behind scrubber doesn’t have to be complicated. At CY Cleaning Equipment, we’re here to help you find the parts you need to keep your scrubber running smoothly. If you need assistance or a fast quote, don’t hesitate to contact us.
By staying ahead of maintenance and ensuring that the right replacement parts are always in stock, you can reduce downtime, extend the life of your equipment, and save on costly repairs.
Happy cleaning!

100AH Lead Acid Battery
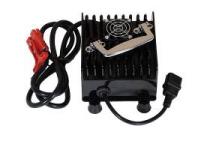
Charger
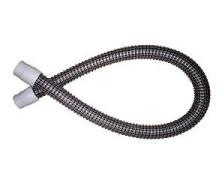
Sewage Suction Pipe
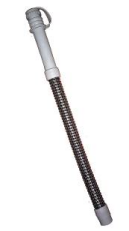
wheels
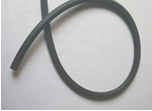
Sewage tank cover seal

Squeege Strip(Red)
.png)
6 Squeege Strip(White)
Brush Motor
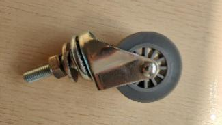
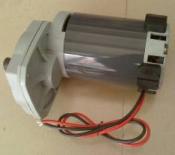
2-inch universal wheel on squeege kit
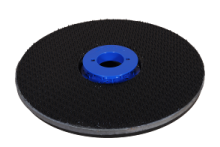
Pad Holder
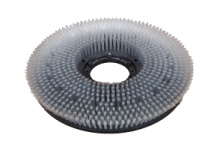
White Cleaning Brush
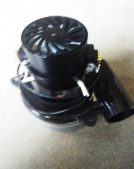
Vacuum Motor
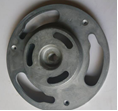
Brush plate fixing buckle
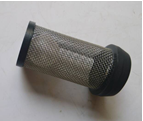
Floating ball net components
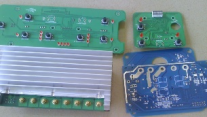
switch assembly
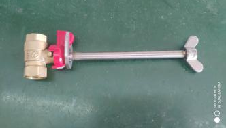
Drain valve with lever
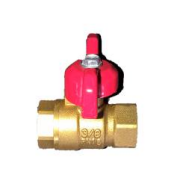
water ball valve
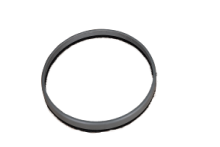
Waterproof cover
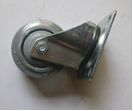
3 inch wheels
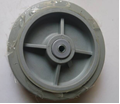
8 inch wheels

water ball valve
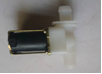
Waterproof cover
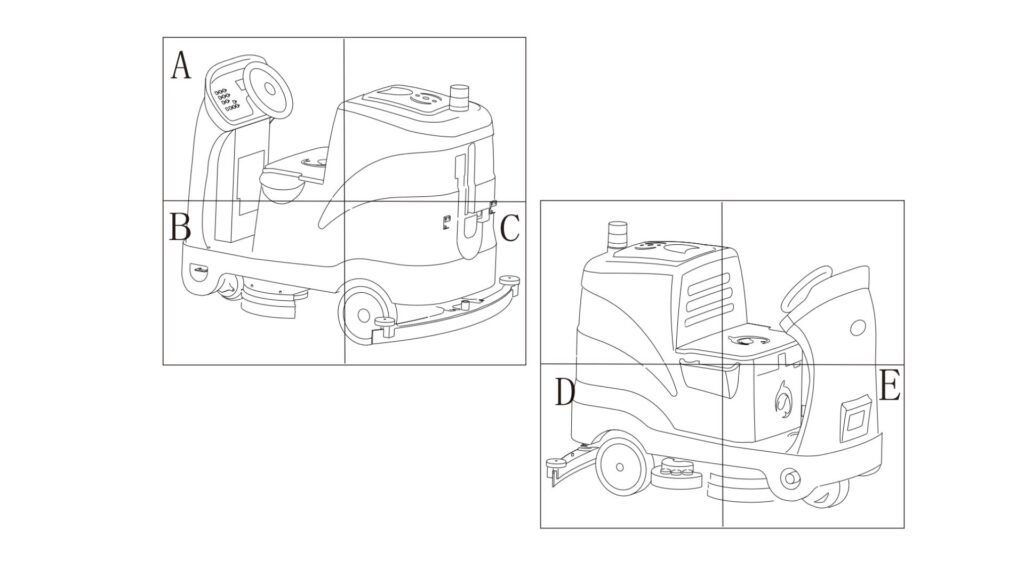
Ride-on Scrubber Maintenance and Repair Spare Parts Checklist That Should Be in Stock: Reduce Downtime & Save Repair Costs
Must-Have Spare Parts for Your Ride-on Scrubber
Here’s a detailed list of the spare parts that are essential to keep in stock for your ride-on scrubber, along with their average usage lifespans, signs of failure, and suggested quantities to keep on hand for the next 2-3 years.
Spare Part | Usage Lifespan | Signs of Wear/Failure | Suggested Quantity for 2-3 Years | Where to Buy |
---|---|---|---|---|
Squeegee Blades | 6-12 months | Streaking, water left on floors, cracks or tears | 4-6 sets (1 set every 6 months) | Shop Squeegee Blades |
Scrub Brushes (Roller Brushes) | 6-12 months | Poor scrubbing performance, frayed bristles | 4-6 sets (2-3 sets per year) | Shop Scrub Brushes |
Pads (Scrub Pads) | 3-6 months | Reduced cleaning efficiency, visible damage or wear | 6-8 sets (2-3 sets per year) | Shop Scrub Pads |
Batteries | 2-5 years | Short battery life, slow charging, doesn’t hold a charge | 2-3 batteries (1-2 every 2-3 years) | Shop Batteries |
Vacuum Motors | 3-5 years | Reduced suction, excessive noise, water left behind | 1-2 motors (1 every 3-5 years) | Shop Vacuum Motors |
Drive Belts | 1-2 years | Scrubber moves slowly, squealing or grinding sounds | 2-4 belts (1 per year) | Shop Drive Belts |
Circuit Boards | 5-7 years | Scrubber won’t start, error codes, irregular operation | 1 circuit board (every 5-7 years) | Shop Circuit Boards |
Water Filtration System | 6-12 months | Clogs, loss of suction, reduced cleaning efficiency | 2-3 filters (1 set every 6 months) | Shop Water Filters |
Recovery Tank Gaskets | 6-12 months | Leaks, inability to properly seal the recovery tank | 2-4 gaskets (1 set every 6 months) | Shop Recovery Tank Gaskets |
Keep your ride-on scrubber running smoothly with our ultimate spare parts checklist. Download now to reduce downtime, save on repairs, and maximize cleaning efficiency.
Introduction
For facilities managers, maintaining a fleet of ride-on scrubbers is crucial to keeping large spaces clean, efficient, and safe. However, these machines—while reliable—require consistent upkeep and timely repairs to ensure they continue to perform at their best. This is where the importance of maintaining a well-stocked inventory of essential spare parts comes into play.
In this comprehensive guide, we’ll walk through the most important ride-on scrubber replacement parts you should keep in stock. We’ll also highlight why each part is critical to the operation of your scrubber, and how having the right parts on hand can reduce costly downtime and save on expensive repair bills.
At the end of this article, we’ve provided a downloadable checklist of the recommended spare parts, so you can keep track of what you need for your fleet and reduce the time your machines spend out of action.
Why Spare Parts Are Essential for Ride-on Scrubbers
Ride-on scrubbers are designed for heavy-duty cleaning in large areas like warehouses, shopping malls, or industrial facilities. As these machines work long hours, they’re more prone to wear and tear compared to smaller models. Having the right spare parts readily available allows you to make repairs quickly, minimizing downtime and extending the lifespan of your equipment.
Here’s why you should maintain a spare parts inventory:
- Avoid Emergency Repairs: Sudden breakdowns can be costly. Having parts ready allows for quick fixes.
- Maximize Efficiency: Regular maintenance ensures your scrubber operates at peak performance, saving both time and energy.
- Reduce Repair Costs: Preventing major breakdowns through early detection of worn-out parts will save you money in the long run.
- Extend Equipment Life: Timely repairs can significantly increase the lifespan of your ride-on scrubber.
Must-Have Spare Parts for Your Ride-on Scrubber
Here’s a detailed list of the spare parts that are essential to keep in stock for your ride-on scrubber, along with their average usage lifespans, signs of failure, and suggested quantities to keep on hand for the next 2-3 years.
Spare Part | Usage Lifespan | Signs of Wear/Failure | Suggested Quantity for 2-3 Years | Where to Buy |
---|---|---|---|---|
Squeegee Blades | 6-12 months | Streaking, water left on floors, cracks or tears | 4-6 sets (1 set every 6 months) | Shop Squeegee Blades |
Scrub Brushes (Roller Brushes) | 6-12 months | Poor scrubbing performance, frayed bristles | 4-6 sets (2-3 sets per year) | Shop Scrub Brushes |
Pads (Scrub Pads) | 3-6 months | Reduced cleaning efficiency, visible damage or wear | 6-8 sets (2-3 sets per year) | Shop Scrub Pads |
Batteries | 2-5 years | Short battery life, slow charging, doesn’t hold a charge | 2-3 batteries (1-2 every 2-3 years) | Shop Batteries |
Vacuum Motors | 3-5 years | Reduced suction, excessive noise, water left behind | 1-2 motors (1 every 3-5 years) | Shop Vacuum Motors |
Drive Belts | 1-2 years | Scrubber moves slowly, squealing or grinding sounds | 2-4 belts (1 per year) | Shop Drive Belts |
Circuit Boards | 5-7 years | Scrubber won’t start, error codes, irregular operation | 1 circuit board (every 5-7 years) | Shop Circuit Boards |
Water Filtration System | 6-12 months | Clogs, loss of suction, reduced cleaning efficiency | 2-3 filters (1 set every 6 months) | Shop Water Filters |
Recovery Tank Gaskets | 6-12 months | Leaks, inability to properly seal the recovery tank | 2-4 gaskets (1 set every 6 months) | Shop Recovery Tank Gaskets |
How to Manage Spare Parts Inventory Effectively
Proper inventory management is key to ensuring you have the parts you need when something breaks down. Here are some tips for managing your ride-on scrubber spare parts inventory:
- Track Part Usage: Keep a log of which parts are most frequently replaced. This helps in identifying the parts you need to prioritize keeping in stock.
- Set Up Reorder Alerts: Implement reorder points for critical items like batteries and squeegee blades to ensure you’re never caught off guard.
- Stock for Multiple Machines: If your facility has several ride-on scrubbers, be sure to stock enough parts for the entire fleet.
- Organize by Part Type: Keep your parts organized by category (e.g., brushes, batteries, motors) for easier access when repairs are needed.
Where to Buy Ride-on Scrubber Parts
At CY Cleaning Equipment, we offer high-quality, durable ride-on scrubber replacement parts that can be shipped quickly to minimize downtime at your facility. We carry everything from squeegee blades to batteries and scrub brushes—all backed by our industry-leading customer service.
Contact us to know our full selection of parts or contact us for more details.
To get available Checklist: Essential Ride-on Scrubber Parts
To help you stay organized and ensure you have everything you need, we’ve created a downloadable checklist of must-have spare parts for your ride-on scrubber. This checklist will make it easier to manage your inventory and ensure you’re prepared for any repairs.
Download the Spare Parts Checklist
Related Articles You Might Find Helpful
- How to Maintain Your Ride-on Scrubber for Maximum Efficiency
- Troubleshooting Common Ride-on Scrubber Problems
- Choosing the Right Ride-on Scrubber for Your Facility
Need Help Finding the Right Part? Contact Us Today!
Having the right spare parts in stock is crucial to maintaining the performance of your ride-on scrubbers. At CY Cleaning Equipment, we’re here to help you with any questions or to provide a quick quote for the parts you need.
Contact us at Cleaning Bling to get started today!
By keeping your ride-on scrubber well-maintained with the right spare parts, you can reduce costly repairs, minimize downtime, and ensure your equipment continues to deliver efficient performance. Download our checklist, stay organized, and enjoy long-lasting equipment reliability.
Happy Cleaning!

120Ah Lead Acid Battery
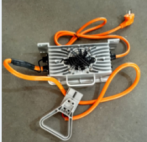
Charger
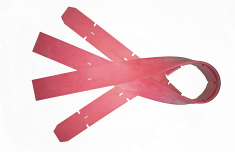
Red Squeege Strip
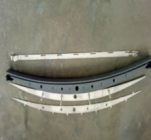
wheels
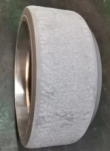
front drive wheels
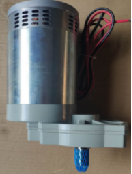
Main brush motor
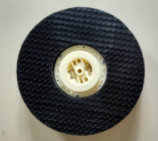
Pad Holder
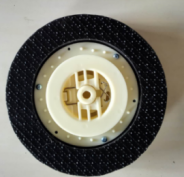
10 inch pad holder
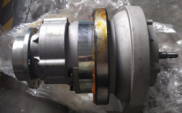
Front drive motor assembly
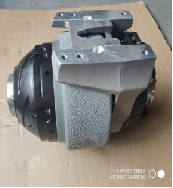
Front drive wheel assembl
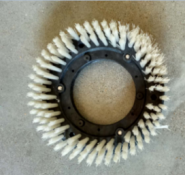
10 inch cleaning brush
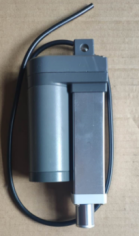
Main push rod motor
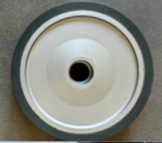
rear wheel

Side brush push rod motor
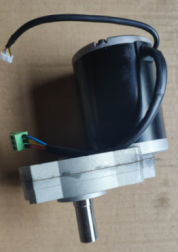
Side brush'motor
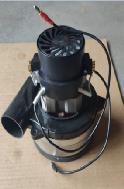
Vacuum Motor
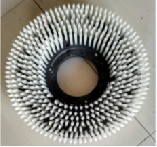
White Cleaning Brush
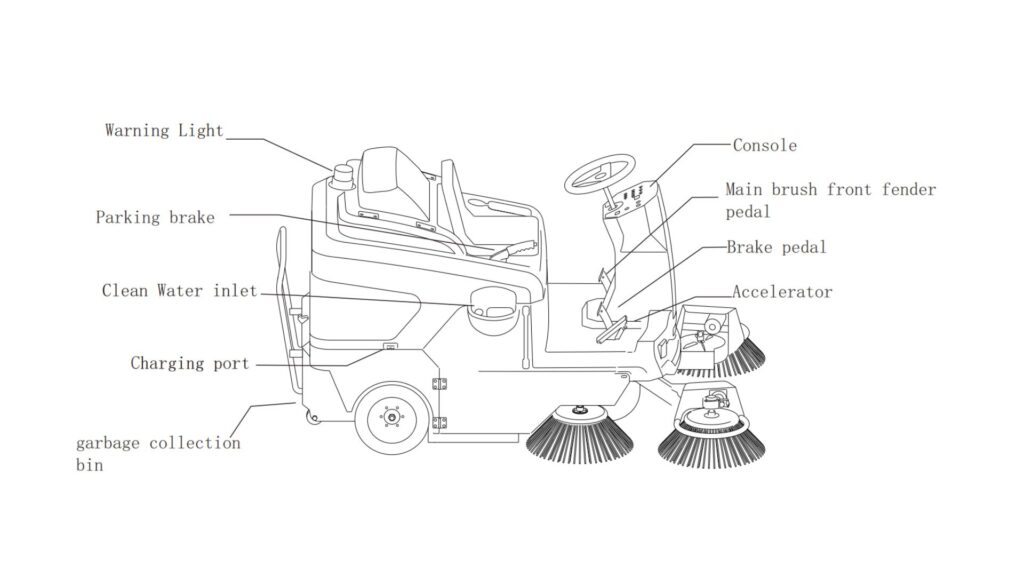
Ride-on Sweeper Maintenance and Repair Spare Parts Checklist that Should Be in Stock: Reduce Downtime & Save Repair Costs
Essential Spare Parts for Ride-on Sweepers
Knowing which parts to keep in stock is the key to avoiding costly downtime. Below is a comprehensive list of essential ride-on sweeper replacement parts, their average usage lifespan, signs of wear, and recommended quantities to have on hand for the next 2-3 years.
Spare Part | Average Lifespan | Signs of Wear/Failure | Suggested Quantity for 2-3 Years | Where to Buy |
---|---|---|---|---|
Main Brushes | 6-12 months | Decreased sweeping performance, visible wear or fraying | 4-6 brushes (1 set per year) | Shop Main Brushes |
Side Brushes | 6-12 months | Uneven or inadequate sweeping, brush bristles breaking off | 6-8 sets (2-3 sets per year) | Shop Side Brushes |
Squeegee Blades | 6-12 months | Water streaks left on floors, tears or cracks | 4-6 sets (1 set every 6 months) | Shop Squeegee Blades |
Batteries | 2-5 years | Short battery life, slow charging, doesn’t hold charge | 2-3 batteries (1-2 every 2-3 years) | Shop Batteries |
Vacuum Motors | 3-5 years | Reduced suction, unusual noises, power loss | 1-2 motors (1 every 3-5 years) | Shop Vacuum Motors |
Drive Belts | 1-2 years | Sluggish operation, noise during operation | 2-4 belts (1 per year) | Shop Drive Belts |
Filters (Air & Dust) | 6-12 months | Clogs, reduced air suction, poor dust collection efficiency | 2-3 filters (1 every 6 months) | Shop Filters |
Circuit Boards | 5-7 years | Unresponsive controls, error messages, system malfunctions | 1-2 circuit boards (every 5-7 years) | Shop Circuit Boards |
Recovery Tank Gaskets | 6-12 months | Leaks, inability to create a proper seal on the recovery tank | 2-4 gaskets (1 set every 6 months) | Shop Recovery Tank Gaskets |
Keep your ride-on sweeper running smoothly with our essential spare parts checklist. Reduce downtime, save on repair costs, and ensure peak performance.
Introduction
In a large facility, keeping everything clean is no small feat. Ride-on sweepers are an essential part of maintaining vast spaces, from warehouses to shopping malls. However, like any piece of machinery that sees heavy use, these sweepers require regular maintenance to avoid downtime. Nothing is more frustrating than a broken sweeper that halts operations.
As a facility manager, it’s essential to ensure that your ride-on sweeper is always in peak working condition. This involves more than just regular maintenance – it requires stocking the right spare parts. By having the most critical parts on hand, you can reduce costly downtime and save on expensive emergency repair costs.
In this guide, we’ll walk you through the must-have spare parts for your ride-on sweeper, including when to replace them, how long they last, and how stocking these parts can help keep your equipment running smoothly.
Why Keeping Ride-on Sweeper Spare Parts Is Essential
Having a spare parts inventory for your ride-on sweeper offers several benefits:
- Reduced Downtime: The longer your equipment is out of action, the higher the cost. Spare parts allow for quick repairs and minimal downtime.
- Cost Savings: Waiting for repairs can be expensive. By fixing minor issues before they become bigger problems, you can save significant amounts in repair costs.
- Enhanced Productivity: Well-maintained equipment ensures your sweepers continue to deliver consistent results, improving overall productivity.
- Prolong Equipment Life: Regularly replacing worn-out parts helps extend the life of your ride-on sweeper, ensuring long-term value.
Essential Spare Parts for Ride-on Sweepers
Knowing which parts to keep in stock is the key to avoiding costly downtime. Below is a comprehensive list of essential ride-on sweeper replacement parts, their average usage lifespan, signs of wear, and recommended quantities to have on hand for the next 2-3 years.
Spare Part | Average Lifespan | Signs of Wear/Failure | Suggested Quantity for 2-3 Years | Where to Buy |
---|---|---|---|---|
Main Brushes | 6-12 months | Decreased sweeping performance, visible wear or fraying | 4-6 brushes (1 set per year) | Shop Main Brushes |
Side Brushes | 6-12 months | Uneven or inadequate sweeping, brush bristles breaking off | 6-8 sets (2-3 sets per year) | Shop Side Brushes |
Squeegee Blades | 6-12 months | Water streaks left on floors, tears or cracks | 4-6 sets (1 set every 6 months) | Shop Squeegee Blades |
Batteries | 2-5 years | Short battery life, slow charging, doesn’t hold charge | 2-3 batteries (1-2 every 2-3 years) | Shop Batteries |
Vacuum Motors | 3-5 years | Reduced suction, unusual noises, power loss | 1-2 motors (1 every 3-5 years) | Shop Vacuum Motors |
Drive Belts | 1-2 years | Sluggish operation, noise during operation | 2-4 belts (1 per year) | Shop Drive Belts |
Filters (Air & Dust) | 6-12 months | Clogs, reduced air suction, poor dust collection efficiency | 2-3 filters (1 every 6 months) | Shop Filters |
Circuit Boards | 5-7 years | Unresponsive controls, error messages, system malfunctions | 1-2 circuit boards (every 5-7 years) | Shop Circuit Boards |
Recovery Tank Gaskets | 6-12 months | Leaks, inability to create a proper seal on the recovery tank | 2-4 gaskets (1 set every 6 months) | Shop Recovery Tank Gaskets |
How to Effectively Manage Your Spare Parts Inventory
Keeping track of your spare parts inventory is vital for ensuring your ride-on sweeper runs without interruptions. Here are some tips for effective inventory management:
- Track Parts Usage: Regularly monitor which parts are replaced most often. This will help you prioritize the parts that you should keep in stock.
- Create Reorder Points: For high-demand parts like batteries and main brushes, set reorder points so that you’re not caught without essential parts.
- Maintain Stock for Multiple Sweepers: If your facility has multiple ride-on sweepers, be sure to maintain enough spare parts to cover your entire fleet.
- Stay Organized: Group similar parts (e.g., filters, brushes, belts) for easy access, and make sure they are clearly labeled.
- Order in Bulk: For parts that have a shorter lifespan, like side brushes and squeegee blades, it might be cost-effective to order them in bulk to save on shipping costs.
Where to Buy Ride-on Sweeper Parts
At CY Cleaning Equipment, we offer an extensive selection of high-quality ride-on sweeper replacement parts, ensuring your machines stay up and running. From vacuum motors to batteries, we carry everything you need to keep your sweepers in top condition.
Visit our online store to shop for the parts you need or reach out to our team for personalized recommendations.
Downloadable Ride-on Sweeper Spare Parts Checklist
We’ve created a downloadable checklist that you can use to keep track of essential spare parts for your ride-on sweeper. This checklist will help you stay organized and ensure you always have the right parts available for maintenance or emergency repairs.
Contact us for the Ride-on Sweeper Spare Parts Checklist
Need Help Finding the Right Part? Contact Us Today!
Having the right spare parts on hand is key to minimizing downtime and ensuring your ride-on sweeper operates at peak efficiency. If you need help finding the right part or want a fast quote, contact CY Cleaning Equipment.
Get in touch with us at Cleaning Bling for all your ride-on sweeper needs.
By keeping your ride-on sweeper well-stocked with essential spare parts, you’ll reduce downtime, save on repair costs, and ensure your equipment is always performing at its best. Download our checklist today and start organizing your spare parts inventory for maximum efficiency!
Happy Sweeping!

Lead Acid Battery
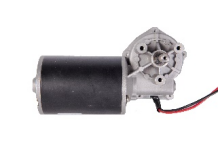
Dust shaking motor
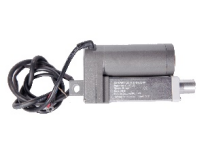
Front side brush lift motor
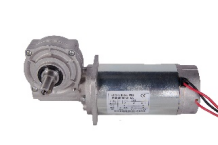
Left brush motor P3
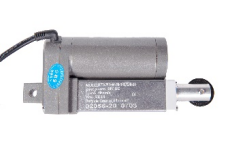
Main brush lift motor
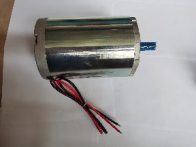
Main brush motor
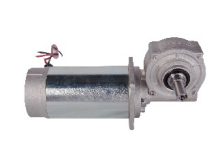
Right brush motor P4
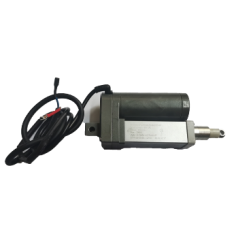
Middle side brush lift motor
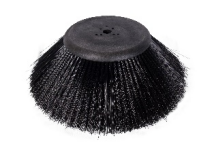
50cm brush
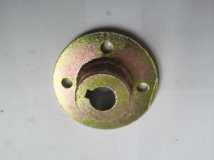
50cm brush flange
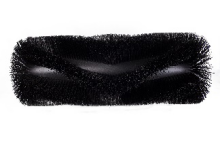
Main brush
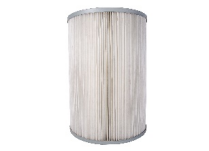
Dust filter
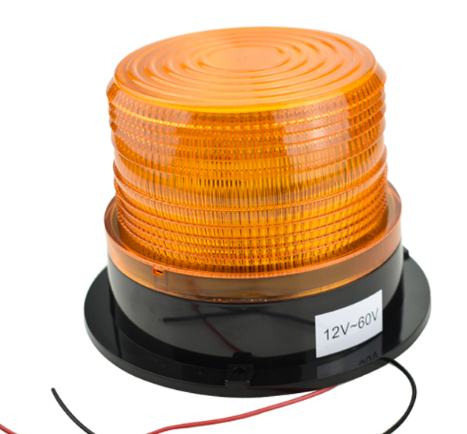
Warning Light
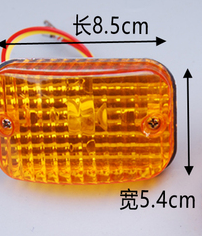
Front signal light
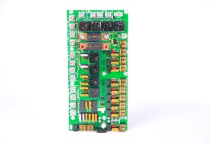
Main control board

Vacuum motor
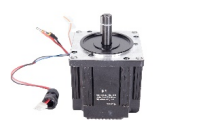
Vacuum motor
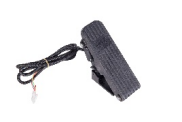
Pedal
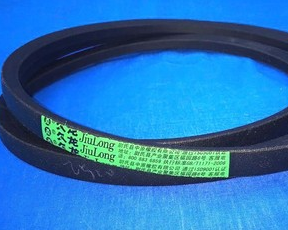
Main brush belt
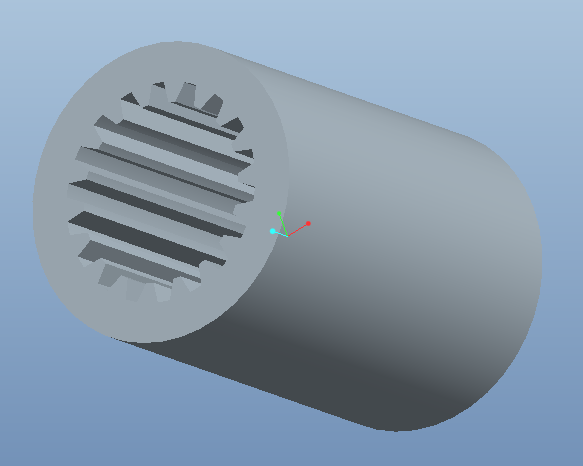
Walking motor connector
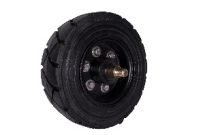
Front tire
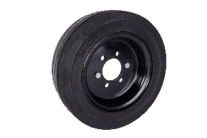
Rear wheel
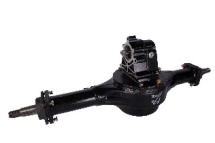
Rear axle differential
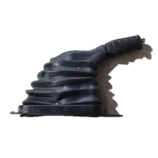
Accelerator
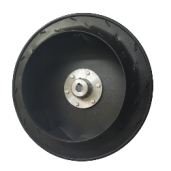
Suction wheel
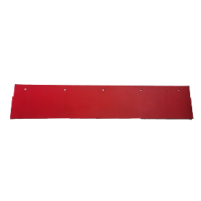
Rear guard strip
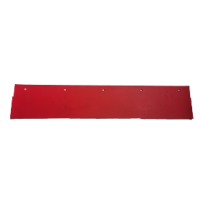
Thick front guard strip
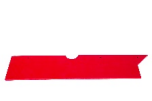
Side water guard strip
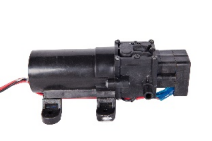
Water pump
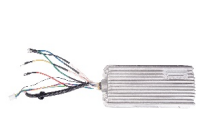
Walking controller
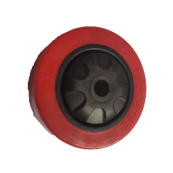
Trash bin 3 inch casters
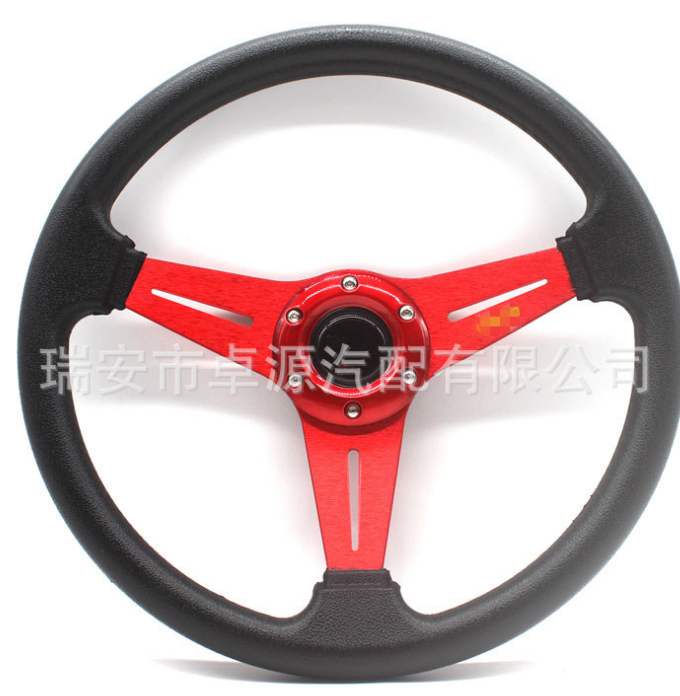
Steering wheel
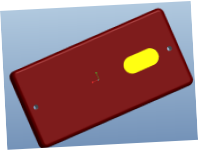
Back signal light
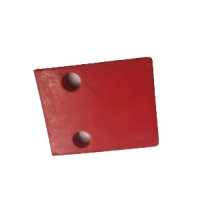
Dust shake film
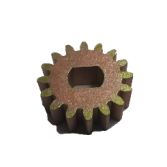
Steering pinion
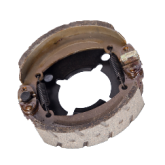
Brake pads with plate
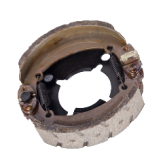
Brake pads without plate
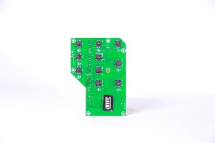
Control panel
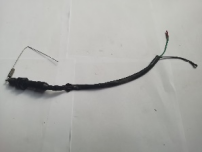
Brake switch
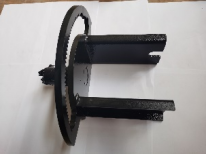
Turn gear
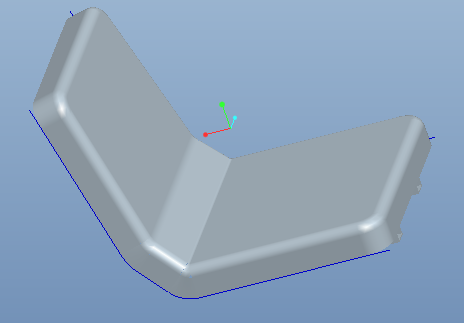
Seat chair
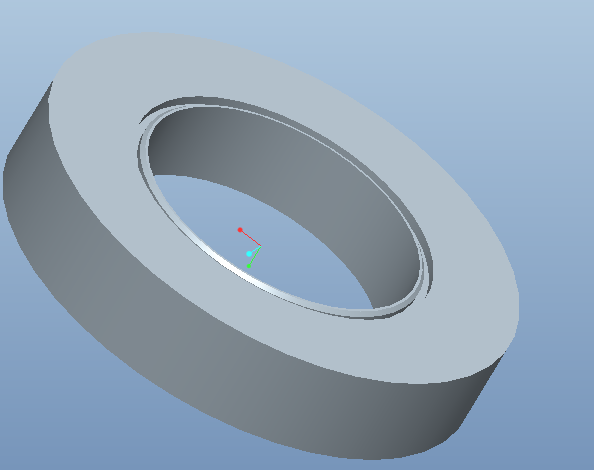
Dust control filter seal
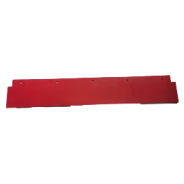
Front water guard strip
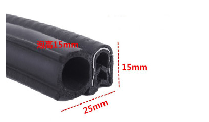
Trash can seal
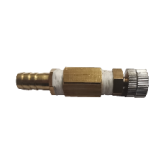
Nozzle
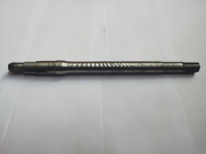
Rear axle long half shaft

Rear axle short half shaft
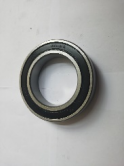
Steering bearing 6010
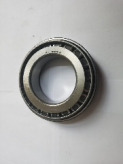
Steering bearing 30206
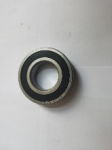
6206 bearing
Floor Scrubber Battery Life: How to Extend It and Reduce Costs
If you manage a large facility, you’ve probably encountered the challenges that come with keeping your floor scrubbers running efficiently. One of the most crucial aspects of ensuring that your floor scrubbers work optimally is extending the battery life. After all, the longer your battery lasts, the fewer disruptions you’ll face in daily operations and the less you’ll need to spend on replacement batteries.
In this article, I’ll walk you through several factors that affect battery life, how to properly maintain your floor scrubber’s battery, and provide solutions to some common battery issues. Plus, we’ll dive into the differences between fast-charging and slow-charging lithium batteries, so you can choose the best option for your business.
Factors Affecting Floor Scrubber Battery Life
Before diving into maintenance and solutions, it’s important to understand the factors that impact battery life. Several elements can determine how long a battery will last, whether you’re using a ride-on floor scrubber with long battery life or a smaller, compact model.
1. Charging Habits
The way you charge your floor scrubber plays a huge role in how long the battery will last. Constantly overcharging or undercharging can significantly shorten its lifespan. Here are a few tips for optimal charging:
- Avoid extreme charging cycles: Try to keep the battery charge between 20-80%. Charging to full capacity all the time can reduce battery life, and depleting it completely can also have negative effects.
- Consider the charging time: If you’re using a ride-on scrubber with long-lasting battery, ensure you’re following the manufacturer’s recommendations for charging times to avoid overloading the battery.
2. Temperature Conditions
The temperature in which the floor scrubber operates has a direct impact on the battery’s performance. High temperatures can lead to overheating, while extremely cold environments will reduce the efficiency of the battery. For example, if you’re working in a warehouse or outdoor area, it’s crucial to store your battery-powered ride-on scrubber in a controlled environment when it’s not in use.
3. Usage Patterns
Your cleaning routine also matters. For example, if the scrubber is constantly pushed to its limits (for example, operating at full power for hours), it will likely drain the battery more quickly. Using it at moderate settings and for appropriate timeframes can extend battery life significantly.
How to Maintain and Extend Your Floor Scrubber’s Battery Life
Now that we know what affects battery performance, let’s dive into how to properly maintain your scrubber’s battery to ensure it lasts as long as possible.
1. Use the Right Battery Type
There are two types of lithium batteries commonly used in ride-on floor scrubbers: fast-charging and slow-charging. Each has its own set of benefits and considerations, so let’s take a look at both.
- Fast-Charging Lithium Batteries: These batteries are designed for quick turnaround times, allowing you to charge your scrubber in as little as 2-4 hours. They’re ideal for businesses with high operational demands or those that need to clean large spaces in short windows of time. For example, our Ride-On Scrubber with Extended Battery Range uses this type of lithium battery, making it perfect for facilities requiring quick cleaning cycles with minimal downtime.
- Slow-Charging Lithium Batteries: These batteries take longer to charge (typically 6-10 hours), but they are gentler on the battery and often last longer over time. They are ideal for facilities that can plan cleaning schedules and don’t mind longer charging times. If your facility operates in shifts, a slow-charging ride-on scrubber for large facilities might be a better fit since it will allow you to extend the life of the battery with careful charging practices.
By choosing the right battery, you’ll not only get the best performance but also maximize the life of your machine and save on maintenance costs.
2. Regular Battery Inspections
It’s crucial to check your ride-on scrubber’s battery regularly for signs of wear and tear. Over time, batteries may show signs of wear, like:
- Corrosion: Battery terminals can corrode, leading to poor connections and potential power loss.
- Leaks: Leaking batteries should be replaced immediately to avoid damage to the scrubber and other components.
- Reduced Performance: If the scrubber isn’t holding a charge or discharges too quickly, it could be a sign that the battery is nearing the end of its life.
Routine inspections help you catch these issues early, saving you from unexpected repairs or replacements.
3. Clean and Maintain Battery Terminals
Keep the battery terminals clean from dirt, dust, and grime. Accumulation of dirt can weaken the connection and reduce the efficiency of the battery. Use a cloth and mild cleaning solution to wipe down the terminals regularly.
Additionally, it’s a good idea to apply a small layer of petroleum jelly to the terminals to prevent rust and corrosion, especially if you’re working in humid or outdoor environments.
Common Battery Issues and How to Fix Them
Even with proper care, battery issues can still arise. Let’s look at some common problems and their solutions:
1. Battery Doesn’t Hold a Charge
This is one of the most common problems with floor scrubber batteries. If the machine doesn’t hold a charge for as long as it used to, here are a few things to check:
- Battery Age: Over time, all batteries lose their capacity. If your scrubber’s battery is older than 2-3 years, it may simply be time to replace it.
- Charger Issues: Sometimes, the problem isn’t with the battery itself but with the charger. Try using a different charger to rule out this possibility.
2. Battery is Overheating
Overheating can lead to serious damage, but it can often be avoided by following good charging practices. If you notice the battery is overheating:
- Check the charging environment: Ensure you’re charging in a well-ventilated space and at the recommended temperatures.
- Use a slower charging cycle: If you’re using a fast-charging lithium battery, consider switching to a slower charge occasionally to give the battery some breathing room.
3. Corrosion on Terminals
Corrosion on the terminals can disrupt the battery’s connection, leading to power loss. Here’s how to fix it:
- Clean the terminals: Use a soft brush or cloth to gently clean the terminals. You can also use a mixture of baking soda and water to neutralize any acid buildup.
Conclusion
Properly maintaining your ride-on floor scrubber battery can save you a lot of money in the long run and ensure your cleaning operations run smoothly. By following the best practices outlined above — including choosing the right battery type, maintaining optimal charging habits, and regularly inspecting your scrubber’s battery — you can extend its lifespan and reduce your overall operational costs.
If you’re interested in a ride-on scrubber with long-lasting battery life, or need more tips on optimizing the performance of your floor cleaning equipment, feel free to explore our selection at www.cleaningbling.com. Eco-friendly scrubbers with lithium batteries are a great investment for businesses that want to keep their costs low while maximizing productivity.
Feel free to explore more on our site for in-depth product comparisons, customer testimonials, and detailed specs to find the best ride-on floor scrubber that fits your business needs!
FAQ: Scrubber and Sweeper Parts and Accessories
If you’re running floor scrubbers and sweepers, you know how vital it is to keep them in top condition. The right parts and accessories can make a massive difference in performance, downtime, and overall cost. Whether you’re new to this industry or a seasoned professional, this FAQ will help answer your most pressing questions about scrubber and sweeper parts.
I’ve worked in this field for years, and trust me, I’ve faced my share of challenges. From choosing the right squeegee to solving battery issues, I’ve been there. Let’s dive in, so you can make informed decisions and keep your machines running like new.
Here’s a quick breakdown of the essentials:
- Squeegees: Used to remove water and cleaning solutions from the floor. Available in rubber or polyurethane materials.
- Brushes: Disk or cylindrical brushes made of nylon, polypropylene, or abrasive materials for tough jobs.
- Filters: Keep dirt and debris from clogging the machine and protect the vacuum motor.
- Batteries: Power the machine, with options like lead-acid or lithium-ion for different performance levels.
- Vacuum Motors: Provide the suction needed for water recovery.
- Tanks: Solution and recovery tanks are critical for holding clean water and collecting waste.
- Hoses: Transport cleaning solutions and suction debris, essential for smooth operation.
- Wheels and Casters: Ensure mobility and machine stability.
If you’re unsure which parts your machine needs, start by consulting the user manual or contacting your supplier.
The lifespan of parts depends on several factors: machine usage, floor types, and maintenance routines. Based on my experience, here’s a general guideline:
- Squeegees: Replace every 3–6 months, depending on wear.
- Brushes: Last between 6 months and 2 years. Regular cleaning extends their life.
- Filters: Clean weekly, replace every 6–12 months.
- Batteries: Lead-acid batteries last 1–3 years; lithium-ion can go up to 5 years.
- Hoses and Wheels: Inspect regularly; replace when signs of wear or cracks appear.
Pro Tip: A good maintenance routine can double the lifespan of many parts. Regularly cleaning tanks, brushes, and filters pays off in the long run.
Signs of wear and tear can sometimes be subtle. Here are a few indicators to watch for:
- Squeegees: Streaks of water left behind indicate they’re worn out.
- Brushes: Flattened bristles or a decrease in cleaning efficiency signal replacement time.
- Filters: Reduced suction power or visible dirt buildup means they need cleaning or replacing.
- Batteries: Shortened runtime or difficulty holding a charge is a red flag.
- Vacuum Motors: Unusual noises or reduced suction could mean it’s time for a check-up.
If you notice these issues, act quickly to avoid further damage or downtime.
Each option has its pros and cons:
- Genuine Parts:
- Made by the original manufacturer.
- Highest compatibility and reliability.
- Usually the most expensive option.
- Best for high-end machines like Tennant, Hako, or CY.
- Aftermarket Parts:
- Produced by third-party manufacturers.
- Often more affordable, with variable quality.
- Ideal for budget-friendly machines or non-critical parts like hoses.
- Reconditioned Parts:
- Used parts refurbished to like-new condition.
- Affordable and eco-friendly but with a shorter lifespan.
- Great for temporary fixes or older machines.
My Take: For mission-critical parts like batteries, motors, or brushes, go with genuine or high-quality aftermarket options. For non-essential components, reconditioned parts can be a smart way to save money.
In a word: yes. High-end machines from brands like Tennant, Hako, Karcher, IPC, Tomcat, or CY are built to last and offer long-term value. Here’s why:
- Durability: Premium materials mean fewer replacements and lower costs over time.
- Performance: Advanced features like imported controllers (e.g., CY machines) ensure efficiency.
- Support: Better customer service and access to OEM parts.
While the upfront cost is higher, the savings in downtime, repairs, and part replacements make it worthwhile.
I know how tempting it can be to cut corners, but trust me, investing in quality pays off. Here are my tips for saving money smartly:
- Buy in Bulk: Stock up on frequently replaced items like brushes and squeegees to take advantage of discounts.
- Routine Maintenance: Proper care can extend the lifespan of most parts.
- Shop Around: Compare quotes from multiple suppliers, but prioritize reliability over price.
- Negotiate: Don’t hesitate to ask for discounts, especially for large orders.
- Partner with Trusted Suppliers: Build relationships with reputable vendors who understand your needs.
A detailed RFQ ensures you get accurate quotes and avoid delays. Here’s what to include:
- Machine Details: Brand, model, and year.
- Part Specifications: Dimensions, materials, and any special requirements.
- Quantity Needed: Specify the number of each part.
- Delivery Requirements: Timeline and location.
- Warranty Expectations: Ask about guarantees on parts.
Pro Tip: The more detailed your RFQ, the better your chances of finding the perfect match for your needs.
Here’s what I look for in a reliable supplier:
- Reputation: Check reviews and ask for references.
- Inventory: A wide selection of parts reduces lead times.
- Expertise: Suppliers with industry knowledge can offer valuable advice.
- Support: Responsive customer service is a must.
- Warranty: Look for suppliers who stand behind their products.
The industry is evolving, with innovations like:
- Smart Parts: Sensors that monitor wear and tear.
- Eco-Friendly Materials: Sustainable options for brushes and filters.
- Longer-Lasting Batteries: Advances in lithium-ion technology.
Keeping up with these trends ensures your machines stay competitive and cost-effective.
Maintaining your scrubbers and sweepers doesn’t have to be a headache. With the right parts, proactive maintenance, and reliable suppliers, you can minimize downtime and maximize performance.
If you’re ready to take the next step, start by reviewing your parts inventory, creating a detailed RFQ, and partnering with suppliers who prioritize your success. Let’s work together to keep your machines running smoothly, one part at a time.
How to Choose the Right Replacement Parts, Accessories and Chemicals for Your Floor Scrubber: A Comprehensive Guide and User Review
If you’re considering purchasing industrial or commercial floor scrubbers or sweepers for your business, it’s important to factor in not only the machine’s performance but also the quality of cleaning agents, accessories, and replacement parts. The combination of the right cleaning solutions, durable parts, and the proper accessories can make a significant difference in both the performance and longevity of your equipment. In this FAQ, I’ll guide you through everything you need to know to make a smart purchase and ensure the floor scrubbers continue delivering outstanding results for years to come.
As you read through this article, you’ll also get to hear from real users, sharing both positive and negative experiences, so you can better understand how these elements affect the overall value of the floor scrubber.
When selecting cleaning solutions for your floor scrubber, it’s important to match the chemical to both the floor type and the cleaning needs. Different chemicals work best for different types of floors, so it’s not a one-size-fits-all situation.
1. Neutral pH Floor Cleaners
These are great for daily cleaning and are typically safe for all types of floors. They clean effectively without damaging the surface or leaving residue behind.
2. Heavy Duty Degreasers
For kitchens, manufacturing plants, or anywhere oil and grease buildup is a concern, heavy-duty degreasers can break down tough grease. These should be used on hard surfaces only.
3. Eco-Friendly Cleaning Solutions
If sustainability is a key concern, opt for eco-friendly solutions made from biodegradable ingredients that won’t harm the environment or your employees’ health.
4. Disinfectants
For high-traffic or healthcare environments, disinfectants are necessary to kill germs and bacteria. Make sure that the disinfectant is safe to use with your floor scrubber.
User Review (Positive):
A warehouse manager shared:
“We use a neutral pH cleaner for our floors, and it’s been great. The scrubber works efficiently with this cleaner, and it leaves the floors streak-free. It’s gentle enough for regular use, but powerful enough to clean effectively.”
User Review (Negative):
A restaurant owner mentioned:
“We once tried a heavy-duty degreaser that clogged our scrubber. The machine got jammed, and it took a while to clean it out. I now avoid strong chemicals unless absolutely necessary.”
Replacement parts are essential for maintaining your floor scrubber’s performance and extending its lifespan. Here’s a breakdown of the most important components you may need to replace over time:
1. Brushes and Pads
The brushes or pads are arguably the most critical part of your scrubber. Over time, they wear down and lose their ability to scrub effectively. Regularly replacing them ensures optimal cleaning performance.
2. Squeegees
Squeegees help collect water and dirt after scrubbing. If they become worn or damaged, they can leave puddles behind, so keep an eye on their condition.
3. Batteries
Battery-operated scrubbers depend on their battery performance. As batteries age, they hold less charge. Replacing batteries promptly can prevent downtime.
4. Filters and Hoses
Filters can clog, and hoses may become worn. Keeping these parts in good condition can prevent water flow problems and ensure the scrubber’s efficiency.
User Review (Positive):
A facility supervisor said:
“We’ve found that replacing the brushes every six months makes a big difference in the cleaning power of our scrubber. It’s an investment that really pays off in performance.”
User Review (Negative):
A commercial cleaning company owner shared:
“We didn’t replace our squeegees in time, and they caused water streaks on the floors. It was a simple fix, but it did lead to some extra work.”
There are a variety of accessories that can improve the performance and convenience of your floor scrubber. Let’s look at some of the most useful ones:
1. Extra Water Tanks
For larger facilities, an additional water tank can help extend cleaning times without having to stop to refill. This is especially useful for long shifts or large areas.
2. Floor Scrubber Trailers
These trailers can be attached to the scrubber to carry more cleaning solution, making it easier to clean large areas without needing to constantly stop and refill.
3. Replacement Battery Packs
If your machine runs on batteries, consider having backup battery packs available. This can minimize downtime in case the current battery is drained during use.
4. Specialty Brushes
Different floor types require different brushes. Soft brushes for delicate floors, medium brushes for general surfaces, and hard brushes for heavy-duty scrubbing. Choosing the right brush can significantly improve cleaning efficiency.
User Review (Positive):
A shopping mall manager shared:
“We added a water tank trailer to our floor scrubber, and it’s a game-changer. We can clean for hours without needing to stop. It saves time and improves productivity.”
User Review (Negative):
A janitorial service provider commented:
“We bought a set of replacement brushes that didn’t fit as expected. It was frustrating because we couldn’t use them right away. Always check compatibility before ordering accessories.”
Eco-friendly cleaning products are growing in popularity as businesses strive to improve their sustainability practices. Here are a few options to consider:
1. Plant-Based Cleaners
These are biodegradable and made from natural ingredients. They are effective for everyday cleaning and are safe for your employees and the environment.
2. Green Seal Certified Products
Green Seal offers certification to cleaning products that meet high environmental standards. Look for their seal to ensure the product is both eco-friendly and effective.
3. Water-Based Cleaners
For light cleaning, water-based cleaners offer a great eco-friendly option. They don’t contain harsh chemicals and are perfect for maintaining a clean and safe environment.
4. Concentrates
Buying cleaning concentrates and diluting them in-house can reduce waste and carbon footprint. You use less packaging, and it’s often more cost-effective in the long run.
User Review (Positive):
A healthcare facility manager mentioned:
“We use a plant-based cleaner in our scrubbers, and we love it. It cleans just as well as traditional chemicals but is much safer for our staff and the environment.”
User Review (Negative):
A hotel cleaning team said:
“We tried an eco-friendly cleaner, but it didn’t have the power we needed to get rid of tough stains. We’ve since switched back to a more powerful solution, but we still look for greener alternatives when possible.”
The right brush makes a significant difference in your cleaning efficiency. When selecting brushes, consider the following:
1. Floor Type
- Soft Brushes are ideal for sensitive or delicate floors like vinyl or polished wood.
- Medium Brushes are best for general-purpose cleaning on tile or concrete floors.
- Hard Brushes work well on rough, gritty surfaces like warehouse or factory floors.
2. Brush Material
Look for brushes made of durable, long-lasting materials. Nylon and polypropylene brushes are often a good choice as they are resistant to wear and tear.
3. Size of Brushes
Make sure the brushes are the correct size for your scrubber. Brushes that are too large or small can affect the machine’s performance and cleaning efficiency.
User Review (Positive):
A retail chain manager shared:
“We’ve found that using medium brushes on our tile floors gives the best results. They clean well without damaging the surface, and they last much longer than the soft ones.”
User Review (Negative):
A facility maintenance worker mentioned:
“We once used hard brushes on our office floors by mistake. They left scratch marks. Always double-check the brush type for the surface you’re cleaning.”
In conclusion, investing in the right cleaning solutions, accessories, and replacement parts can significantly affect the overall performance and longevity of your floor scrubber. The CY floor scrubber, for example, is known for its reliable performance and low maintenance costs. By using the right chemicals, regularly replacing key parts, and choosing accessories that enhance your cleaning efficiency, you ensure that your investment continues to deliver high value over time.
Remember, good value is not just about the upfront price—it’s about choosing equipment and products that will serve you well in the long run. Keep these tips in mind, and you’ll be set for smooth, effective floor cleaning operations in your business.
Need Help? Contact Us Now!
Looking for top-quality scrubbers and sweepers for industrial & commercial use from Chinese Leading manufacturer?
Talk about your needs.