Walk-behind Floor Scrubber
Innovative cleaning equipment to maximize efficiency and minimize cost.
Reliable Floor Cleaning Machines – Factory Direct & Built to Last
Keep Your Business Clean with High-Quality, Reliable Machines.
Our advanced floor cleaning machines are engineered for maximum efficiency, helping businesses maintain spotless environments with less effort and cost.
Walk-behind floor scrubbers are ideal for cleaning medium to large areas up to 26,00 square meters per hour efficiently.
DC520 | Battery Auto Scrubber 20 in
DC520 autoscrubbers are high speed, maintenance free, battery autoscrubbers that deep cleans floors up to 19,375 square feet per hour. The DC520 machines features a cast aluminum 20″ head with single brush powered by best-in-class motors. High capacity solution and recovery tanks make for long operation before refilling. Industry leading vacuum motors and large floor squeegee leaves floors totally clean & dry.
DC510 | Battery Auto Scrubber, 20 in
DC510 autoscrubbers are high speed, maintenance free, battery autoscrubbers that deep cleans floors up to 19,375 square feet per hour. The DC520 machines features a cast aluminum 20″ head with single brush powered by best-in-class motors. High capacity solution and recovery tanks make for long operation before refilling. Industry leading vacuum motors and large floor squeegee leaves floors totally clean & dry.
DC50B | Battery Auto Scrubber 20 in. Traction Drive
DC510 autoscrubbers are high speed, maintenance free, battery autoscrubbers with traction function that deep cleans floors up to 40,364 square feet/ 3500 sq meters per hour. The DC50B machines features a cast aluminum 20″ head with single brush powered by best-in-class motors. High capacity solution and recovery tanks make for long operation before refilling. Industry leading vacuum motors and large floor squeegee leaves floors totally clean & dry.
Unique Features:
Top brand Lithium battery with high battery life and 3-year warranty.
Reliable quality for 5-10+ years lifetime.
IoT-enabled to improve efficiency and reduce costs, that allows you to monitor, control, and optimize remotely.
High-speed cleaning, water-saving technology, and durable construction.
High-powered motors, automated cleaning functions, and low maintenance costs.
Eco-friendly operation, and user-friendly interface.
High-capacity tanks, precision cleaning, and easy maintenance.
Customer Review:

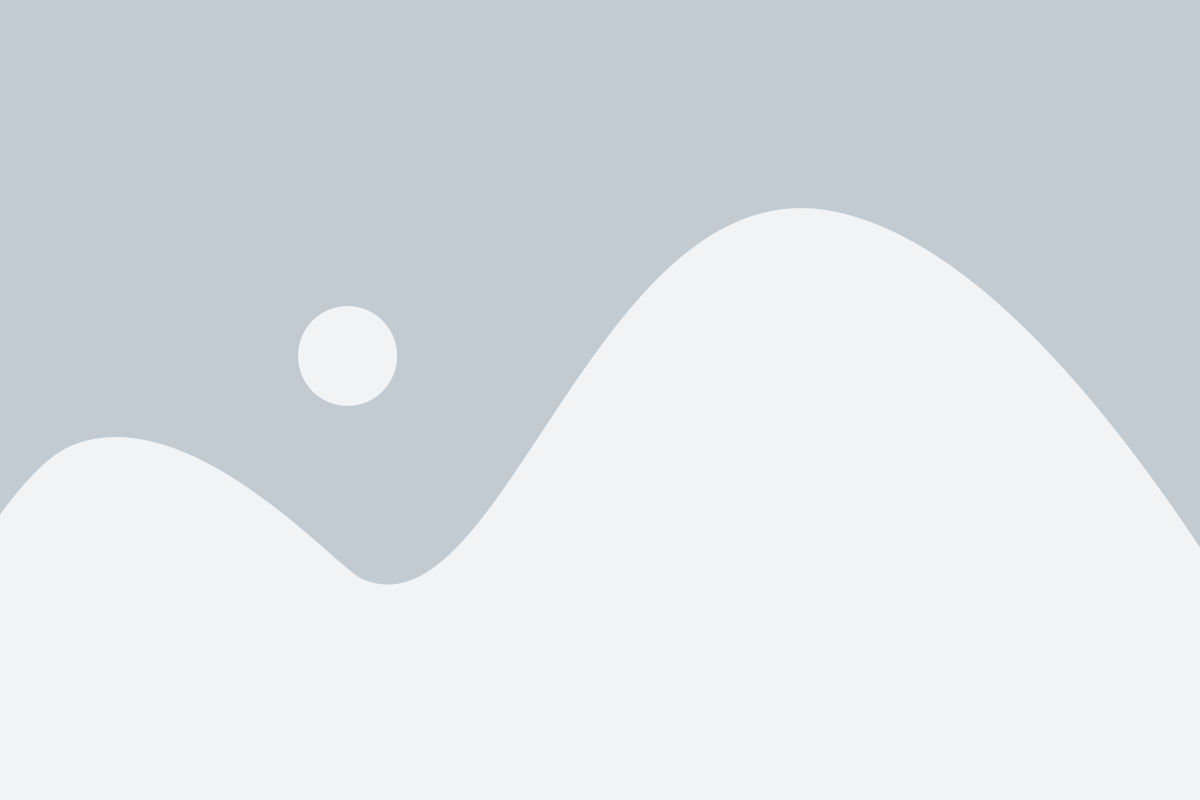
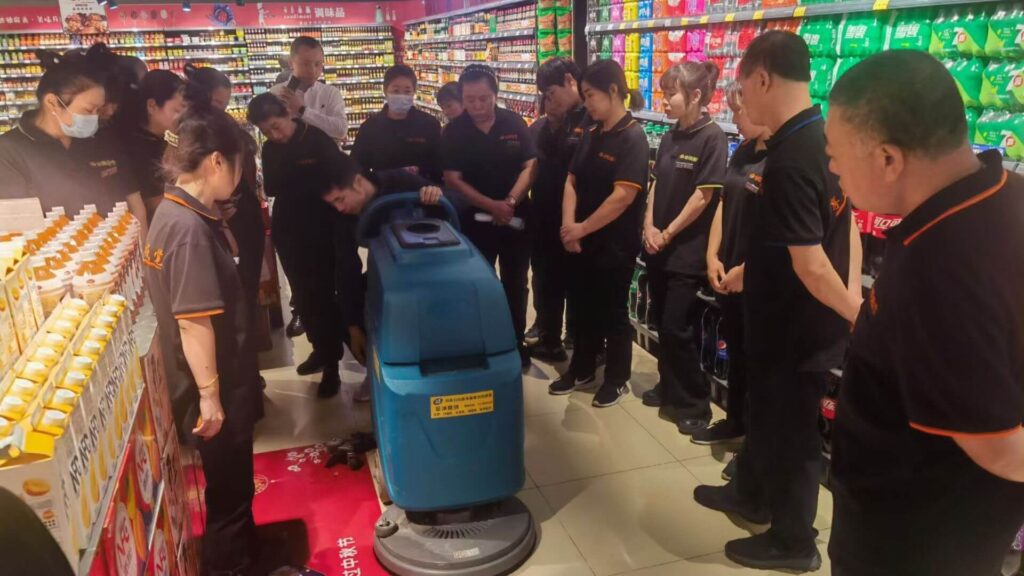
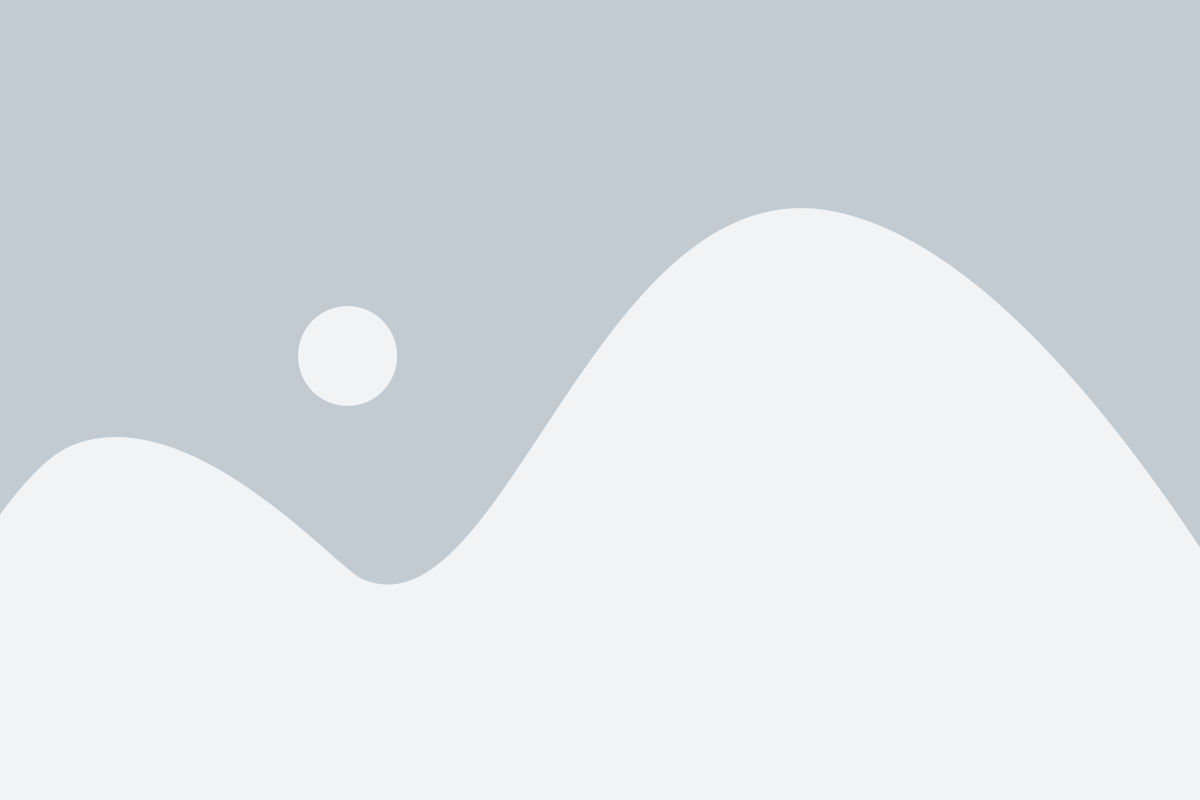

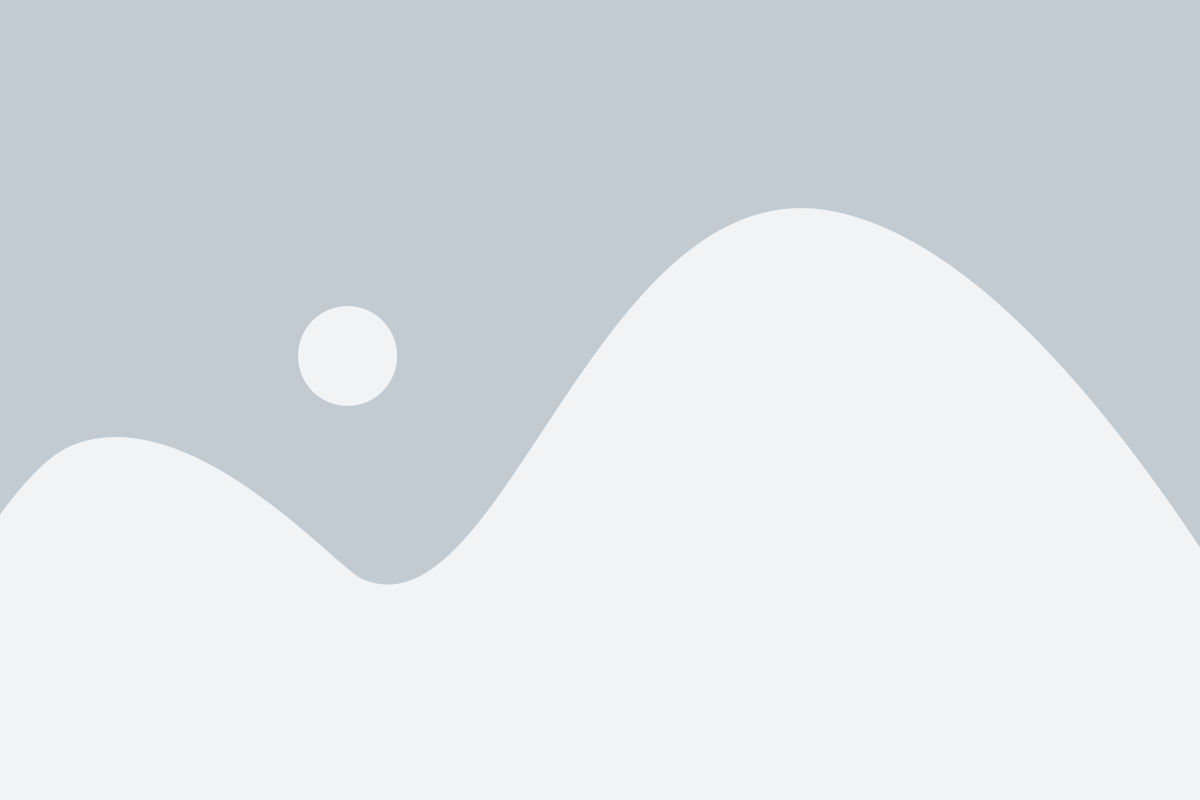
Customer Testimony: 6-Year-Old CY Cleaning Equipment Still Going Strong
💬 If You’ve Ever Thought, “Will This Cleaning Machine Last?” — Read This First
I remember walking into a large railway station in Guiyang a few years ago — one of our clients had installed a CY Cleaning floor scrubber there back in 2017. This wasn’t a clean, polished showroom. It was a bustling transportation hub, with thousands of daily footfalls, oily residues, wet tracks, and constant grime.
Naturally, I was curious. Six years had passed. How was the machine holding up?
The maintenance manager smiled and said something I’ll never forget:
“It’s still going strong. Six years, two shifts per day, and the scrubber hasn’t let us down once.”
As someone who works inside a floor cleaning equipment factory, I can’t tell you how proud that made me. This was a real-world test — not a lab simulation. And the machine passed with flying colors.
If you’re looking for a machine that truly lasts, or wondering if our claims as a floor cleaning solutions supplier hold water — this article is for you.
Let me show you what six years of real use looks like with CY Cleaning Equipment
🛠️ Real Case: 6 Years of Daily Use — No Downtime, No Drama
Let’s talk specifics.
In 2017, the Chongqing West Railway Station ordered several CY scrubbers for daily cleaning operations. These units were used across large platforms, corridors, and public restrooms — clocking in multiple hours per day under heavy use.
What’s incredible is not just that they’re still working. It’s that they’re still working flawlessly.
✨ No motor replacements
✨ No structural damage
✨ Only basic wear-and-tear parts like squeegee blades or filters needed refreshing
The customer told us:
“The machines are like soldiers — clean, quiet, and dependable.”
This is what it means to work with a professional floor cleaning machine manufacturer. We’re not just selling you equipment — we’re building machines that become a part of your team.
⚖️ Industry Reality: Most Machines Fail by Year 3–4
Before joining CY, I worked in facility management, and I’ve used equipment from many commercial floor cleaning equipment suppliers.
Here’s the uncomfortable truth:
- Most floor scrubbers start losing efficiency by year three
- Parts begin to fail, and repairs get expensive
- Teams end up spending more on downtime and maintenance than the machine itself
This is what we set out to change when we built CY — a company grounded in real-world reliability, not marketing promises.
As a floor cleaning equipment factory, we control everything — from the sourcing of durable materials to rigorous QC testing. That’s how we get machines to last twice as long as the industry average.
🔍 So, Why Do CY Machines Last So Long?
Let me walk you through what we do differently:
✅ 1. Industrial-Grade Components
We don’t use generic parts. As an industrial floor cleaning solutions manufacturer, we engineer every system — from drive motors to water tanks — to withstand daily punishment in large-scale facilities.
✅ 2. User-Friendly Maintenance
Our scrubbers are built by people who use scrubbers. That means quick access to filters, easy-to-clean recovery tanks, and parts that swap out in minutes — not hours.
✅ 3. Reinforced Build Quality
Our machines use steel-reinforced frames and rust-resistant coatings. They don’t warp, crack, or rattle over time. Even after six years, many machines still look like new.
✅ 4. Battery Management Tech
On our battery-powered models, smart charging logic protects the battery life. Customers report up to 5–7 years of battery performance with proper care.
🧼 Maintenance Tips from a Factory Insider
I often get asked: “What can I do to make my CY machine last even longer?”
So here’s what we tell all our clients — whether you’re running a hospital or a hardware store:
- Drain water daily — avoid buildup in the dirty water tank
- Rinse the squeegee and filter weekly — it keeps the motor happy
- Avoid overcharging batteries — unplug when full
- Check hoses for clogs monthly
- Store indoors — protect against weather and sun
These basic practices, when paired with CY quality, are why our machines are still cleaning after 6, 8, even 13 years.
📣 Quotes That Speak Louder Than Specs
Here’s what some of our customers had to say:
🗣️ “Five years in and the machine still sounds like it did on day one.”
🗣️ “We’ve tried other brands, but only CY delivered that ‘like-new’ feel after all these years.”
🗣️ “Your scrubber outlasted our last three cleaning managers.” (Yes, that was a joke… but kind of not.)
🌎 Who We Work With
As a floor cleaning machine manufacturer, our clients span a wide range of industries:
- 🏥 Hospitals & Healthcare — where hygiene matters most
- 🚉 Airports & Rail Stations — where reliability is non-negotiable
- 🏬 Malls & Retail Chains — where aesthetics drive brand value
- 🏭 Factories & Logistics — where grime, dust, and oil are daily challenges
Our mission isn’t just to make machines — it’s to help you keep your floors spotless, your operations smooth, and your costs low.
📈 The ROI: Why It Matters to You
Think about this: a cheap scrubber that dies after 3 years costs you not just money, but lost time, labor, and peace of mind.
Now imagine a CY scrubber that runs like new after six years.
No downtime. No emergency service calls. No surprise part failures.
That’s real return on investment. That’s the power of choosing a company that’s more than just a floor cleaning tools manufacturer — but your long-term partner.
✅ In Summary: What You Can Expect from CY Equipment
- Machines that last 5–10+ years
- Support directly from the floor cleaning equipment factory
- Quality control from a top-tier floor cleaning solutions supplier
- A team that’s with you before, during, and after your purchase
🚀 Final CTA: Looking for Equipment That Stays Strong Year After Year?
If you’re ready to stop cycling through unreliable machines every few years…
If you want a scrubber or sweeper that your staff will still be using years from now…
Then it’s time to meet CY.
👉 Explore our full line of machines.
We’re not just building floor cleaning tools — we’re building your next favorite employee.
Let’s talk. Let’s clean. And let’s make your equipment investment last.
Specifications-Comparative Overview
Model
Product Function:
Operation Mode:
Drive Typ:
Control Panel
Install & Remove Brush
Cleaning Width
Squeegee Width
Working Efficiency
Brush Pressure
Brush RPM
Brush Head
Battery Type
IoT-Enable
Vacuum Motor
Brush Motor:
Traction Motor
Solution Tank
Recovery Tank
Machine Dimension
DC510
Floor Cleaning
Walk-Behind Pad Assist
Manual Push
Intelligent Control Panel
Automatic
20″/510mm
33″/850mm
19,375 SqFt/h (1800Sqm/h)
35KG
180RPM
Cast aluminum, sigle brush
Lead-acid/Lithium Maintenace-free
Yes
550 watt
480 watt
N/A
17 Gallon / 65L
17 Gallon / 65L
55″L x 24″W x 41″H (140cmx62cmx105cm)
DC50B
Floor Cleaning
Walk-Behind Traction Drive
Traction Drive
Mechanical Control Panel
Manual
20″/510mm
33″/850mm
40,364 SqFt/h (3750Sqm/h)
35KG
180RPM
Cast aluminum, sigle brush
Lead-acid/Lithium Maintenace-free
Yes
550 watt
480 watt
380 watt
17 Gallon / 65L
17 Gallon / 65L
55″L x 24″W x 41″H (140cmx62cmx105cm)
DC520
Floor Cleaning
Walk-Behind Pad Assist
Manual Push
Mechanical Control Panel
Manual
20″/510mm
33″/850mm
19,375 SqFt/h (1800Sqm/h)
35KG
180RPM
Cast aluminum, sigle brush
Lead-acid/Lithium Maintenace-free
Yes
550 watt
480 watt
N/A
17 Gallon / 65L
17 Gallon / 65L
55″L x 24″W x 41″H (140cmx62cmx105cm)
🧠 Key Differentiators
- DC510: Designed for standard cleaning tasks, offering reliable performance with a 20-inch cleaning path and manual push operation.NorTex Sales & Service+6wisconsinscrubandsweep.com+6Cleaning Equipment Direct+6
- DC520: Similar to the DC510, it provides consistent cleaning efficiency, suitable for environments where manual operation is preferred.
- DC50B: Equipped with a traction drive, it significantly increases cleaning capacity, making it ideal for larger areas requiring efficient and effortless operation.JaniSource, LLC
🧩 Suggested Use Cases
- DC510: Best suited for small to medium-sized facilities such as retail stores, offices, and schools where maneuverability and ease of use are essential.
- DC520: Ideal for environments similar to those of the DC510, offering consistent performance for routine cleaning tasks.
- DC50B: Perfect for large commercial spaces like warehouses, shopping malls, and airports where high cleaning capacity and reduced operator fatigue are priorities.
IoT Floor Scrubbers in Multi-Site Operations: Managing Cleaning Performance Across Locations
All CY Cleaning Floor Scrubbers and Sweeprs are IoT-Enabled.
Comparison: Traditional vs. IoT-Enabled Scrubbers
Feature | Traditional Scrubber | IoT Floor Scrubber |
---|---|---|
Data Collection | Manual, paper-based | Automatic, real-time |
Compliance Monitoring | On-site inspections required | Remote dashboard access |
Maintenance Alerts | Reactive (after failure) | Predictive alerts before failure |
Reporting | Labor-intensive | One-click export |
Enterprise Integration | Not supported | API-ready, scalable |
ROI Timeline | 12–18 months | 6–9 months |
Discover how IoT-enabled floor scrubbers empower enterprises and property managers to streamline operations, enhance smart management, and achieve remote monitoring across all locations.
Why I Believe IoT is the Missing Link in Your Multi-Site Cleaning Strategy
A few years ago, I was consulting for a national property management firm that operated more than 50 retail locations. Their biggest headache wasn’t dirty floors—it was inconsistent cleaning quality, lack of transparency, and costly site visits to “check” performance.
That’s when I introduced them to our IoT-enabled floor scrubbers from CY Cleaning Equipment.
Within months, their KPIs improved:
✔️ Better cleaning consistency
✔️ Less manual reporting
✔️ Real-time accountability
If you’re managing several facilities, you know what I mean—what works in one location might be falling apart in another. That’s where IoT changes everything.
What Is an IoT-Enabled Floor Scrubber?
An IoT-enabled floor scrubber is a smart cleaning machine embedded with sensors and wireless connectivity. It automatically collects and transmits performance data such as:
- Operation time
- Area cleaned
- Water/detergent usage
- Battery health
- Error logs
That means you don’t have to rely on manual checklists or onsite supervision anymore. The scrubber tells you what’s happening, when it happens.
At CY Cleaning Equipment, our IoT scrubbers integrate seamlessly into enterprise management platforms, making remote monitoring simple—even across 100+ locations.
Why It Matters for Multi-Site Operators
If you’re overseeing cleaning teams across cities—or even countries—you’ve likely faced these issues:
- ✅ Inconsistent cleaning outcomes
- ✅ High labor turnover
- ✅ Lack of compliance proof
- ✅ Expensive on-site inspections
- ✅ Delays in maintenance
A traditional floor scrubber can’t solve that. But an IoT floor scrubber? It becomes part of your data ecosystem.
Smart Management with IoT: Centralized Control, Decentralized Execution
One of our largest clients—a national logistics center—recently equipped 18 warehouses with CY’s smart floor scrubbers. They were able to monitor every cleaning cycle remotely, using our web dashboard that pulls real-time data from each unit.
Here’s how IoT transforms your cleaning ops:
📊 Real-Time Dashboards
Track usage, errors, and productivity across sites from your laptop or phone. This reduces the need for site managers to chase cleaning logs or report performance.
📍 Location-Based Monitoring
Know exactly when a machine was used and where. Each floor scrubber uploads its location history, so you can verify site compliance without lifting a finger.
🛠️ Predictive Maintenance
Machine acting up in one of your 12 buildings? You’ll know before it breaks. IoT data flags declining performance and alerts you instantly—helping you schedule service proactively.
🕑 Labor Efficiency
Reduce dependency on manual oversight. With automation, your staff knows they’re being tracked for quality, which often results in a 15–25% increase in cleaning compliance.
Use Cases Across Industries
Industry | IoT Use Case |
---|---|
Retail Chains | Monitor in-store floor cleaning consistency |
Airports & Stations | Schedule off-hour scrubbing and remotely verify zone coverage |
Manufacturing Plants | Prevent downtime with predictive scrubber maintenance |
Commercial Real Estate | Provide clients with digital cleaning reports as part of your SLA |
Healthcare Facilities | Validate disinfection protocols with timestamped cleaning logs |
View our latest case studies here
Comparison: Traditional vs. IoT-Enabled Scrubbers
Feature | Traditional Scrubber | IoT Floor Scrubber |
---|---|---|
Data Collection | Manual, paper-based | Automatic, real-time |
Compliance Monitoring | On-site inspections required | Remote dashboard access |
Maintenance Alerts | Reactive (after failure) | Predictive alerts before failure |
Reporting | Labor-intensive | One-click export |
Enterprise Integration | Not supported | API-ready, scalable |
ROI Timeline | 12–18 months | 6–9 months |
Image Gallery: CY IoT Scrubbers in Action
Model A – Compact IoT Scrubber for Retail | Model B – Industrial-Grade for Warehouses |
Browse our full product range here: www.cleaningbling.com/products
How We Built Smart Scrubbing Into CY’s DNA
When we developed our IoT series at CY Cleaning Equipment, we didn’t just bolt on sensors. We built the architecture to scale across multi-site operations.
Our IoT models integrate with:
- Secure cloud servers (hosted in AWS or localized options)
- Mobile & desktop dashboards
- Enterprise cleaning software (custom API access available)
- Maintenance partner platforms for automatic dispatch
Want to test a unit in your facility? Contact us for a free trial program.
FAQs: IoT-Enabled Floor Scrubbers
Q: Do I need internet access at every location?
A: No. Our scrubbers can store offline data and sync when reconnected.
Q: Is data secure?
A: Yes, we use encrypted data protocols and offer private cloud options for enterprises.
Q: Can IoT scrubbers integrate with my existing CMMS or ERP?
A: Yes. We offer open APIs and support most facility management systems.
Final Thoughts: The Future of Multi-Site Cleaning Is Now
If you’re managing cleaning across 3, 30, or 300 locations, you need tools that scale with you. CY’s IoT-enabled floor scrubbers help you remove the guesswork, improve visibility, and optimize your cleaning force from a single screen.
And you don’t have to take a leap of faith—we’re here to support you with implementation, onboarding, and performance analytics.
👉 See our full IoT scrubber range: https://cleaningbling.com/product/
📩 Download our enterprise whitepaper: Smart Cleaning at Scale
📞 Book a free virtual demo: Schedule Now
Let’s clean smarter, together.
🚶♂️ Traction Power Walk-Behind Scrubbers DC50B: Special Use Cases
Traction-powered scrubbers use a motorized drive system to assist forward and backward movement. This eliminates the need for manual pushing, offering significant advantages in specific scenarios:
✅ 1. Large-Area Cleaning
- Why it matters: Operators can clean for longer periods without fatigue.
- Examples: Warehouses, airports, shopping malls, convention centers, and logistics centers.
- DC50B fit: Its traction drive and high sq ft/hr capacity (40,364) make it ideal for these environments.
✅ 2. Sloped or Uneven Surfaces
- Why it matters: Manual scrubbers are difficult to control on inclines or uneven flooring.
- Examples: Parking garages, industrial ramps, and facilities with graded surfaces.
- Traction benefit: Motorized movement ensures consistent control and cleaning effectiveness.
✅ 3. Extended Operation Time
- Why it matters: In environments that require prolonged cleaning shifts, operator fatigue becomes a risk.
- Examples: Hospitals, schools, and manufacturing facilities operating multiple shifts.
- Advantage: Reduces physical strain on workers, leading to higher productivity and fewer errors.
✅ 4. Heavier Cleaning Loads
- Why it matters: When the scrubber carries more water or battery weight, manual models can become hard to maneuver.
- Examples: Food production plants, large supermarkets, and distribution centers.
- Benefit: Traction drive handles added weight with ease, maintaining maneuverability.
✅ 5. ADA-Compliant & Inclusive Work Environments
- Why it matters: Makes cleaning tasks accessible to a wider range of employees, including those with limited physical strength.
- Examples: Government or corporate facilities focused on inclusive labor practices.
- Traction impact: Reduces the physical barrier to using professional-grade cleaning equipment.
Manual Push vs. Traction Drive Walk-Behind Scrubbers: Which Is Right for Your Facility?
CY DC50B is Traction Drive Walk-behind scrubber.
What’s the Difference?
Feature | Manual Push Scrubber | Traction Drive Scrubber |
---|---|---|
Propulsion | Operator must push manually | Motorized wheels move the machine |
Operator Effort | Higher; physically demanding on large surfaces | Lower; minimal physical effort required |
Speed Control | Fixed (based on operator pace) | Adjustable speed via control panel |
Initial Cost | Lower | Higher due to added motor components |
Best For | Small to medium spaces (<1,500 m²) | Medium to large facilities (1,500–5,000+ m²) |
Fatigue Level | Moderate to High | Low |
Maintenance | Simple | Requires basic motor and electronics maintenance |
Choosing between a Manual Push walk-behind scrubber and a Traction Drive walk-behind scrubber? This guide compares both to help you find the perfect fit for your cleaning operation.
Introduction: A Real Decision I Had to Make
Let me take you back a few years. As someone who’s worked in cleaning equipment industry servicing across many industries—from logistics centers to schools—I remember being stuck in the same spot you are now: Should I go with a manual push scrubber or invest in a traction drive model?
Back then, I underestimated how much that decision would impact productivity, operator fatigue, and overall cost efficiency. So, if you’re facing this same choice today, let’s break it down together—clearly, honestly, and with insights that’ll actually help.
What Are Walk-Behind Scrubbers?
Walk-behind scrubbers are floor-cleaning machines designed for facilities that need regular, reliable, and efficient cleaning. Unlike mop-and-bucket methods, scrubbers clean and dry the floor in one pass.
There are two main types:
- Manual Push Walk-Behind Scrubber – The operator pushes it manually.
- Traction Drive Walk-Behind Scrubber – The machine propels itself forward via a motor, reducing operator effort.
Both are available from manufacturers like CY Cleaning Equipment, known for durability and innovation in cleaning machinery.
What’s the Difference?
Feature | Manual Push Scrubber | Traction Drive Scrubber |
---|---|---|
Propulsion | Operator must push manually | Motorized wheels move the machine |
Operator Effort | Higher; physically demanding on large surfaces | Lower; minimal physical effort required |
Speed Control | Fixed (based on operator pace) | Adjustable speed via control panel |
Initial Cost | Lower | Higher due to added motor components |
Best For | Small to medium spaces (<1,500 m²) | Medium to large facilities (1,500–5,000+ m²) |
Fatigue Level | Moderate to High | Low |
Maintenance | Simple | Requires basic motor and electronics maintenance |
Use Cases: When Each Type Makes Sense
✅ When a Manual Push Walk-Behind Scrubber is Right
If your team cleans smaller facilities like:
- Clinics or small retail shops
- Classrooms or office corridors
- Cafeterias or lobbies under 1,500 m²
Then a manual push model may be a perfect fit. It’s simple, cost-effective, and gets the job done without unnecessary complexity.
👉 See our Manual Scrubber Lineup to find a match for your square footage.
✅ When a Traction Drive Walk-Behind Scrubber is Worth It
For larger facilities, the time and energy saved by using traction drive scrubbers is a game changer:
- Warehouses and factories
- Large educational institutions
- Hospitals and airports
- Shopping malls
I remember one client who switched from manual to traction and reduced labor time by 40%. Their team no longer complained of back pain, and they cleaned more space in less time—with fewer breakdowns thanks to the machine doing the heavy pushing.
👉 Learn more about our Traction-Drive Scrubbers and how they reduce total cost of ownership over time.
Why Your Decision Matters
This isn’t just about wheels or motors. It’s about your:
- Operational efficiency
- Staff morale
- Cleaning results
- Long-term ROI
Choosing the right machine means:
✅ Less downtime
✅ Happier cleaning staff
✅ Lower risk of accidents or muscle strain
✅ Faster cleanups = lower labor costs
Real-World Comparison: A Logistics Facility Case Study
One of our customers in a 4,000 m² logistics hub in Shenzhen had been using a manual push walk-behind scrubber. The results?
- 3 staff required per shift
- 5+ hours to clean the entire area
- High operator fatigue = high turnover
After switching to a traction drive model from CY Cleaning Equipment, they:
- Cut cleaning time to 2.5 hours
- Needed only 2 operators
- Increased floor shine rating based on internal audits
Their investment paid off in just 6 months.
Key Benefits Summary
🚶♂️ Manual Push Walk-Behind Scrubber – Pros & Cons
Pros:
- Affordable upfront cost
- Easy to maintain
- Compact and simple to operate
Cons:
- Physically demanding
- Slower for large areas
- Limited automation
🔋 Traction Drive Walk-Behind Scrubber – Pros & Cons
Pros:
- Less operator fatigue
- Adjustable speeds
- More efficient for large areas
Cons:
- Higher upfront investment
- Slightly more complex maintenance
Our Recommendation: Think Long-Term
If your facility is under 1,500 m² and budget is tight, a Manual Push walk-behind scrubber is an excellent starting point.
But if you’re cleaning large spaces, multiple shifts a day, or want to reduce turnover and boost efficiency, a Traction Drive walk-behind scrubber is hands-down the better choice.
Both models are available with water-saving features, low-noise motors, and easy-to-clean tanks via our Product Catalog.
Still Not Sure?
You’re not alone—we help dozens of businesses every month navigate these decisions. Our team at CY Cleaning Equipment can provide:
- Free ROI calculators
- On-site demos
- Case studies from your industry
📩 Reach out via our Contact Page or download our latest Product Comparison Guide (PDF).
Final Thoughts: Cleaning Shouldn’t Be a Struggle
As someone who’s been in the field, I can tell you—cleaning is already tough work. The right equipment shouldn’t make it harder. Whether you’re managing a warehouse, school, or showroom, the right choice between manual push and traction drive walk-behind scrubbers can free up your team’s energy to focus on what matters: results.
And if you’re still debating, why not give both a test drive? We’d love to help you compare models firsthand.
Brush Head Cast Aluminum Walk-Behind Scrubbers: Why Durability and Precision Matter in Industrial Cleaning
All CY Walk-behind scrubbers are equipped with Cast Aluminum Cast Brush head.
Side-by-Side Comparison: Cast Aluminum vs. Traditional Scrubbers
Feature | Plastic Scrubber | Stamped Steel Scrubber | Cast Aluminum Scrubber |
---|---|---|---|
Structural Integrity | Weak under heavy load | Can warp or corrode | Exceptionally strong and durable |
Weight | Lightweight but fragile | Heavy and cumbersome | Lightweight yet solid |
Corrosion Resistance | Low | Moderate | High – resists rust & chemicals |
Long-Term Cost | Frequent repairs | Prone to wear | Lower TCO (Total Cost of Ownership) |
Operator Comfort | Often unstable | Hard to maneuver | Stable and easy to control |
Discover how a brush head cast aluminum walk-behind scrubber delivers unmatched industrial scrubber durability, cleaning precision, and ROI for demanding commercial environments.
Built to Last: Why Material Quality Isn’t Optional in Industrial Cleaning
When I first started working with industrial clients—warehouses, logistics centers, factories—one of the first questions I’d hear wasn’t “How fast is it?” or “What’s the cleaning width?” It was always:
“Will it last?”
And they were right to ask.
Industrial cleaning environments are unforgiving. Floors are rough, shifts are long, and breakdowns cost more than just repair fees—they cost time, trust, and productivity. That’s why we designed the brush head cast aluminum walk-behind scrubber with one principle in mind: durability is not a feature—it’s a necessity.
What Is a Brush Head Cast Aluminum Walk-Behind Scrubber?
Let’s start with the basics.
A brush head cast aluminum walk-behind scrubber is an industrial-grade cleaning machine with a scrubbing head constructed from cast aluminum, not plastic or stamped metal. It’s guided by an operator walking behind the unit, offering precise maneuverability and surface control. The cast aluminum construction gives it a rigid, long-lasting foundation that outperforms other materials in high-stress cleaning environments.
And trust me, once you’ve used one, there’s no going back.
Why Cast Aluminum Makes All the Difference
As someone who’s seen machines wear down far too early, I can tell you: material matters. Here’s why cast aluminum outperforms the alternatives:
✅ Strength Without the Weight
- Cast aluminum offers high tensile strength but remains relatively light, reducing operator fatigue.
- Perfect for high-maneuverability applications without compromising durability.
✅ Corrosion Resistance
- Unlike steel, cast aluminum won’t rust, even when exposed to detergents, humidity, or water over time.
- Great for wet environments or chemical-heavy cleaning routines.
✅ Precision Manufacturing
- Because it’s molded rather than stamped or bent, cast aluminum allows for tighter tolerances and smoother operation—you can actually feel the difference in performance.
- That precision translates to more consistent floor contact, better cleaning, and longer brush life.
Where Durability Meets ROI: Industrial Scrubber Durability in Action
We’ve sold our CY Cast-Pro Series scrubbers across a wide range of industries, and I’ve had the privilege of walking factory floors with facilities managers who put these machines to the test—literally.
Here’s what they told me:
- “The plastic models cracked within 12 months. Your cast aluminum units? Still solid after 3 years.”
- “Maintenance costs dropped by nearly 40%.”
- “Operator satisfaction went up. The machine just feels like a quality build.”
And I get it. When a machine doesn’t rattle or flex under pressure, you trust it more. That trust is the difference between cutting corners and cleaning with confidence.
Side-by-Side Comparison: Cast Aluminum vs. Traditional Scrubbers
Feature | Plastic Scrubber | Stamped Steel Scrubber | Cast Aluminum Scrubber |
---|---|---|---|
Structural Integrity | Weak under heavy load | Can warp or corrode | Exceptionally strong and durable |
Weight | Lightweight but fragile | Heavy and cumbersome | Lightweight yet solid |
Corrosion Resistance | Low | Moderate | High – resists rust & chemicals |
Long-Term Cost | Frequent repairs | Prone to wear | Lower TCO (Total Cost of Ownership) |
Operator Comfort | Often unstable | Hard to maneuver | Stable and easy to control |
Who Should Be Using a Cast Aluminum Walk-Behind Scrubber?
If you’re managing any of the following facilities, you’ll see a huge impact:
🏭 Heavy-Duty Manufacturing
Tight spaces, chemical spills, grease—these environments demand a machine that can withstand intense use without downtime.
🚚 Warehouses & Logistics
Long shifts and constant traffic mean you need a machine that won’t buckle under daily use. Durability here translates to uninterrupted workflows.
🛠️ Maintenance Contractors
Service providers need reliable, easy-to-transport machines they can trust from site to site. Cast aluminum gives you the peace of mind you need.
Explore all of our walk-behind scrubber options to see which model fits your exact need.
A Closer Look: CY Cleaning’s Cast Aluminum Technology
At CY Cleaning Equipment, we’re not new to innovation. Our cast aluminum brush heads are precision-crafted in-house, tested under extreme stress, and engineered with:
- Reinforced rib structures for torque resistance
- Thermally stable casting for consistent scrub pressure
- Anodized coatings for added corrosion defense
We’ve made it a point to control every part of the process, and the results speak for themselves.
Product Spotlight:
CastPro-900: Compact, cast aluminum brush head for tight spaces | CastPro-1200: Heavy-duty version with extended tank capacity |
FAQs: Brush Head Cast Aluminum Walk-Behind Scrubbers
Q: Will cast aluminum crack under pressure?
A: No. Cast aluminum is designed to absorb stress without warping or cracking—perfect for rugged environments.
Q: Is maintenance harder than with plastic units?
A: Actually, it’s easier. Because cast aluminum doesn’t flex or break, you’ll spend less time dealing with wear-related issues.
Q: Are these machines heavier?
A: Not significantly. In fact, most users report better balance and maneuverability due to the stable center of mass.
Let’s Talk About Your Needs
Durability isn’t a luxury. In industrial cleaning, it’s a requirement.
If you’re tired of replacing plastic heads, repairing bent frames, or answering complaints from cleaning staff, it might be time to upgrade to a brush head cast aluminum walk-behind scrubber. You’ll get more life, more value, and more control.
🔗 Explore our full industrial lineup here: www.cleaningbling.com/products
📩 Want to talk specs or get a quote? Contact our team today
Final Thoughts: Built for the Long Haul
I’ve seen machines that look good in brochures fall apart on day 90. And I’ve seen our cast aluminum scrubbers humming like new after year two.
So when I tell you that brush head cast aluminum walk-behind scrubbers can transform your cleaning operation, I mean it—not just as a manufacturer, but as someone who’s stood on those floors, solving the same problems you’re facing now.
Let’s build a cleaner, smarter, tougher future—together.
How to Maintain Your Floor Cleaning Machine: Expert Tips on After-Sales Support and Repairs
Keeping your floor cleaning machines in top condition is crucial for ensuring they run efficiently and last for years. Whether you are using a floor cleaning machine with warranty and support or managing a fleet of machines for commercial use, understanding how to properly maintain your equipment and knowing when to reach out for technical support for floor cleaning machines can save you time, money, and frustration in the long run. In this article, we’ll provide you with expert tips on how to care for your cleaning machines and the importance of after-sales service to keep your machines running smoothly.
1. Why Maintenance Matters for Floor Cleaning Machines
When you invest in floor cleaning equipment, you’re not just purchasing a machine—you’re investing in the efficiency and cleanliness of your operations. Whether it’s a scrubber dryer or sweeper, these machines perform complex tasks that, when maintained properly, can significantly improve your productivity. On the other hand, when they are not cared for, they may experience downtime, leading to expensive repairs, interruptions in your cleaning schedule, and ultimately, frustration.
Maintaining your floor cleaning equipment isn’t just about preventing issues—it’s also about extending the lifespan of the machine. Regular maintenance can help you avoid high repair costs and ensures that your cleaning solutions continue to perform at their best.
2. Routine Maintenance: The Key to Longevity
The best way to prevent breakdowns and minimize repair costs is through routine maintenance. Here are some essential upkeep tasks you should carry out regularly:
a. Clean and Replace Brushes
The brushes are critical for effective cleaning. Over time, they accumulate dirt, debris, and wear out. Regularly check and clean your brushes to ensure optimal performance. If the brushes are worn or damaged, replace them immediately. This small task can help prevent more significant issues with your floor cleaning machine parts and accessories later on.
b. Check and Maintain the Battery
For battery-powered machines, check the battery regularly. Keep the terminals clean and ensure that the battery is charged properly. If your machine runs on a lead-acid battery, make sure to top up the water levels regularly. A well-maintained battery ensures that your machine operates efficiently, and the battery’s life is prolonged.
c. Inspect the Vacuum System
The vacuum system plays an essential role in floor cleaning machine performance. Ensure the suction hoses are clear of any blockages. Cleaning filters regularly and replacing worn-out seals will maintain the suction power and prevent unnecessary strain on the motor.
d. Monitor the Fluid Levels
Floor cleaning machines often use a combination of water, cleaning solution, and sometimes even specific oils. Regularly check and replace fluids, such as solution tank water or oil, as needed. This prevents issues related to low fluid levels, which can lead to inefficient cleaning or machine malfunctions.
3. When to Seek After-Sales Support
No matter how diligent you are about maintaining your equipment, there will be times when your machine needs professional attention. Here are some signs that it’s time to seek help from your floor cleaning machine repair services or a professional technician:
a. Unusual Noises or Vibrations
If your machine is making loud or irregular noises, this could be a sign of internal damage. Don’t ignore these signs! The longer you wait, the more extensive the repair may become. Get in touch with technical support for floor cleaning machines to help you identify the problem.
b. Poor Cleaning Performance
If your floor cleaning machine is no longer picking up dirt or leaving streaks behind, it’s an indication that something may be wrong. A professional inspection will help you diagnose the issue—whether it’s a malfunctioning motor, damaged brushes, or clogged suction systems.
c. Leaking Fluids
Fluid leaks are a red flag. If you notice that your machine is leaking water, solution, or oil, it’s critical to seek immediate help. Leaks not only affect performance, but they can also lead to more significant damage to the machine’s internal components.
d. Electrical Issues
If your machine won’t turn on, or it suddenly powers off during use, there may be an electrical problem. Electrical issues should always be handled by professionals to avoid further damage or safety risks.
4. The Role of Spare Parts in Keeping Your Machine Running
When it comes to repairs, using quality spare parts for floor cleaning machines is crucial. High-quality parts ensure the longevity and efficiency of your machine. It’s always a good idea to rely on your floor cleaning equipment supplier for genuine parts to avoid the risks associated with aftermarket components. Whether it’s a replacement motor, brush, or suction fan, genuine parts are specifically designed to fit your machine and work in harmony with its other components.
By maintaining a stock of essential floor cleaning machine parts and accessories, you can avoid delays in repairs and ensure your machine is always ready for use.
5. Why You Should Invest in Comprehensive After-Sales Support
The importance of comprehensive after-sales support for floor cleaning machines cannot be overstated. A reliable support team can offer troubleshooting, repairs, and provide guidance when you face issues. Here’s why this support matters:
a. Access to Expertise
Having a dedicated team to assist with repairs means you have access to experts who understand the inner workings of your machines. These professionals can diagnose and resolve issues more efficiently than anyone else, saving you time and ensuring your machine performs optimally.
b. Reduced Downtime
Downtime is costly, especially for businesses that rely on their floor cleaning machines to maintain a clean environment. When you have reliable customer service for floor cleaning solutions, any issues can be resolved quickly, minimizing the amount of time your equipment is out of commission.
c. Peace of Mind with Warranty
Many floor cleaning machines come with a warranty, which means that repairs or replacements of certain parts can be covered under this guarantee. Having a strong after-sales service team means you can make the most of these warranties without hassle.
d. Long-Term Cost Savings
By having access to ongoing support, you can avoid expensive repairs that may arise from neglect or improper maintenance. The sooner you can identify a problem, the less likely it is to escalate into a costly fix.
6. Testimonials: Real Stories from Customers
Here’s what some of our customers have to say about our floor cleaning machine repair services:
“I’ve been using CleaningBling’s machines for years, and the after-sales service has been a game changer. Whenever we face any issues, their technical support team is quick to respond and gets us back on track in no time.” – Jake T., Facilities Manager
“The spare parts provided by CleaningBling have always been top-quality. It’s reassuring to know that the parts I’m using to repair our machines are durable and specifically designed for our models.” – Sarah L., Business Owner
7. Conclusion
Maintaining your floor cleaning machines is essential for keeping your operations running smoothly and avoiding costly downtime. By performing regular maintenance and knowing when to seek help from professional repair services, you can extend the life of your equipment and ensure that it continues to deliver optimal performance. Make sure to take advantage of after-sales support and rely on genuine spare parts to keep your machines in excellent condition.
At CleaningBling, we’re dedicated to providing not just the best floor cleaning machines, but also comprehensive after-sales support to help you troubleshoot, repair, and maintain your equipment. If you have any questions or need assistance, don’t hesitate to reach out to our customer service for floor cleaning solutions.
For more information on how to maintain your floor cleaning equipment and access our range of services, contact us today.
Maximize Efficiency with Your Floor Scrubber: Tips from Real Users and Experts
When you are in the market for industrial and commercial floor scrubbers and sweepers, it’s crucial to make an informed decision. Whether you are considering equipment for a large facility, a retail store, or a warehouse, selecting the right model can significantly impact your cleaning operations, efficiency, and bottom line. But what does it take to make the best choice?
Let’s dive into this comprehensive FAQ, where we explore some of the key aspects of selecting the right floor scrubber. We’ll include best practices, real user reviews, and tips for maximizing the performance of your equipment. We’ll also make sure to cover what truly makes a floor scrubber a good value—from pricing and quality to maintenance and performance.
Best practices for operating a floor scrubber are essential for maximizing cleaning efficiency and ensuring the longevity of your equipment. Here are some tips that can save you time, money, and frustration:
Tip 1: Pre-clean the floor surface
Before using the scrubber, make sure the floor is free from large debris, like stones or paper, to avoid damage to the scrubber’s brushes and to achieve optimal results.
Tip 2: Use the correct settings for different floor types
Adjust the water level and scrub speed according to the type of floor you are cleaning (e.g., tile, concrete, or hardwood). Using the correct settings ensures maximum efficiency and prevents unnecessary wear on your equipment.
User Review:
A retail store owner shared:
“We learned quickly that adjusting the scrubber’s speed based on the surface type made a huge difference in how quickly we could clean and how clean the floors looked afterward. It took some trial and error, but we’ve got it down now!”
Tip 3: Regularly maintain the machine
Make sure to clean the scrubber’s brushes and replace worn parts regularly. This helps keep the machine working at its best and prevents breakdowns.
Maximizing efficiency with your floor scrubber is all about using the machine to its full potential while keeping operational costs low. Here’s how to get the most out of your investment:
Tip 1: Plan your cleaning route
Before starting, map out the areas you need to clean. Follow a consistent pattern to ensure you’re not wasting time by retracing steps.
Tip 2: Use the right detergent
For stubborn stains, use a cleaning solution designed for your type of floor. Choosing the right detergent can reduce the need for multiple passes, increasing efficiency.
Tip 3: Adjust the machine’s settings
Make sure you’re using the optimal water and detergent settings for the type of dirt and the floor surface. Too much water can lead to excess drying time, while too little water might not clean thoroughly.
User Review:
A warehouse manager explained:
“When we first started using our scrubber, we had to make multiple passes over the same spots to get the floors clean. Once we started adjusting the detergent levels and water flow, we noticed a significant improvement in cleaning time.”
However, a business owner in the food processing industry pointed out:
“Maximizing efficiency was a bit challenging at first, especially when dealing with grease. It took time to figure out the right detergent mix, but once we did, the cleaning time was cut in half.”
Why it’s important for good value:
By maximizing your scrubber’s efficiency, you reduce labor costs and cleaning time, both of which contribute to long-term savings. The CY scrubber, for example, is known for its consistent performance and low maintenance, allowing you to get more work done in less time, boosting overall productivity.
Not all floor types require the same treatment. It’s important to use the right technique and settings for various surfaces. Here are some tips to ensure your floor scrubber works effectively across multiple types of flooring:
Tip 1: For smooth floors (e.g., tiles, marble)
Use a low-speed scrub to avoid damaging the surface. Gentle scrubbing will remove dirt without leaving streaks.
Tip 2: For rough, textured floors (e.g., concrete, textured vinyl)
Increase the scrub pressure and use a stronger cleaning solution to remove embedded dirt and grime. These floors are more durable, so you can use a higher scrubbing speed and pressure.
Tip 3: For delicate surfaces (e.g., wood, laminate)
Make sure to use a soft brush and avoid excess water, as it could damage the surface. A low-speed scrubber is key here.
User Review:
A customer with a fleet of cars in an automotive shop shared:
“We have both concrete floors and painted floors in our shop. The scrubber works well on the concrete, but we had to adjust the brush pressure and reduce the water flow on the painted floors to avoid chipping the paint.”
However, a facility manager in a hospital had a different experience:
“We use the scrubber on a variety of floors, including marble and vinyl. The difference in surface materials means I have to adjust the settings a lot, which can be time-consuming.”
Why it’s important for good value:
Using the scrubber correctly on different surfaces ensures you achieve optimal results without damaging the floors or the machine. Models like the CY floor scrubber come with adjustable settings for different surfaces, making them versatile for a wide range of environments, from retail spaces to food processing facilities.
A good value floor scrubber isn’t just about a lower price—it’s about performance, durability, and ongoing savings. Here’s what makes the CY floor scrubber a solid investment:
Reason 1: Reliable Quality
The CY scrubber is built with imported controllers that ensure consistent, high-performance cleaning for over 5 years. This is critical when looking for equipment that will serve you long-term without frequent breakdowns.
Reason 2: Quiet Operation
The low-noise design of the CY scrubber allows for cleaning in areas where noise could be disruptive, such as office buildings or retail spaces, without disturbing workers or customers.
Reason 3: Easy Maintenance
The CY scrubber is easy to operate and maintain, which reduces your downtime and minimizes maintenance costs. With low failure rates and affordable parts for replacement, it ensures you get more value for your investment.
Reason 4: Long Battery Life
The long battery life of the CY scrubber means you can clean large areas in one go, reducing the need for multiple charge cycles.
Reason 5: Excellent After-Sales Service
The professional and timely after-sales service means that you can rely on prompt support whenever needed, which ensures minimal disruption to your cleaning schedule.
In summary, the right floor scrubber isn’t just about the initial purchase price. The CY floor scrubber exemplifies good value by offering a combination of durability, low maintenance costs, versatility across different surfaces, and efficient performance. By following best practices and using the right settings for different surfaces, you can maximize the efficiency of your floor scrubber and enjoy long-term savings.
Ultimately, choosing the right floor scrubber is about finding a balance between quality, cost, and functionality. With the CY scrubber, you’re investing in a machine that offers excellent performance, reduced downtime, and a reputation for reliability, ensuring you get the most value over the long term.
Need Help? Contact Us Now!
Looking for top-quality scrubbers and sweepers for industrial & commercial use from Chinese Leading manufacturer?
Talk about your needs.